Why does an alternator fail sooner than expected? It’s a common question for anyone dealing with machinery maintenance. These causes of alternator failure can lead to costly breakdowns if not caught early.
As an Electrical Engineer specializing in alternators, I’ve seen these problems many times. With years of experience, I know what can go wrong and how to fix it.
Here are 2 of the most common reasons that lead to alternator failure:
- Worn Out Bearings
- Faulty Voltage Regulator
In this guide, you’ll learn about these and other common causes, breaking down exactly what leads to alternator failure and how you can prevent it.
Let’s get started!
1. Quick Overview
Alternator failure can occur for many reasons, often leading to unexpected downtime and costly repairs. Understanding these causes helps prevent problems and maintain efficient performance. Below are the top 10 causes of alternator failure for a quick reference:
Cause | Problem | Solution |
Worn Out Bearings | Bearings wear down due to friction or lack of lubrication. | Replace bearings regularly to maintain smooth rotation. |
Faulty Voltage Regulator | Regulator can’t control voltage properly. | Replace faulty regulators promptly. |
Worn Out Brushes | Brushes wear from constant friction. | Replace brushes as they wear down. |
Excessive Heat | Heat damages internal parts of the alternator. | Maintain cooling systems around the alternator. |
Loose or Worn Belt | Belts become loose or worn over time. | Adjust or replace belts when necessary. |
Electrical Overload | Too much demand causes alternator strain. | Limit connected devices to reduce load. |
Damaged Wiring | Wires wear or corrode, causing poor connections. | Replace damaged wiring promptly. |
Leaking Fluids | Fluids seep into the alternator, causing damage. | Fix leaks quickly to protect internal components. |
Faulty Diodes | Diodes fail, causing poor power conversion. | Replace worn or damaged diodes. |
Excessive Alternator Load | Overloading the alternator leads to overheating. | Reduce load or upgrade to a higher-capacity alternator. |
2. Worn Out Bearings
Worn-out bearings are a common issue that can cause alternator to break down. Bearings allow the alternator to spin smoothly, but over time, they can wear out. Here are some common reasons why this happens:
Dirt and Debris
- Problem: Dust, dirt, or small particles can get inside the alternator, causing friction and wear on the bearings. This makes it harder for the alternator to spin properly.
- Solution: Use a sealed alternator to keep debris out or clean the area regularly to prevent buildup.
- Tip: Keep your machinery and surroundings free from excessive dust or dirt to avoid damaging the bearings.
Lack of Lubrication
- Problem: Bearings need lubrication to move smoothly. Without enough lubrication, they will dry out, overheat, and cause grinding, which leads to faster wear.
- Solution: Use high-quality lubricants and apply them during regular maintenance to keep the bearings moving freely.
- Tip: Set a schedule for lubrication checks, especially in hot or dusty environments, to avoid running the alternator dry.
Improper Installation
- Problem: If bearings are installed incorrectly, they can become misaligned, creating extra pressure and causing early failure. This can happen during repair or replacement.
- Solution: Always check alignment carefully when installing new bearings or the alternator.
- Tip: Follow the manufacturer’s installation guide step by step to avoid unnecessary stress on the bearings.
3. Faulty Voltage Regulator
A voltage regulator manages the electricity the alternator produces. If it fails, the alternator won’t charge properly. According to research, the faster the alternator spins, the more power it generates, making regulation crucial. Here are some common reasons this happens:
Electrical Overload
- Problem: Running too many electrical devices at once can overload the voltage regulator, making it struggle to control voltage levels.
- Solution: Limit how many high-power devices are connected at one time to avoid putting too much strain on the regulator.
- Tip: Check the power usage of all connected devices regularly to prevent overloads.
Old or Worn Parts
- Problem: Over time, the parts inside the voltage regulator can wear out, leading to poor performance or failure. This often happens with older machines.
- Solution: Replace the voltage regulator as soon as it starts showing signs of wear or unstable voltage.
- Tip: Schedule regular checks to catch worn regulators early, especially in older equipment.
Loose Connections
- Problem: Loose wires or poor connections can cause the voltage regulator to malfunction, leading to inconsistent voltage control.
- Solution: Tighten all connections during routine maintenance to keep the regulator working smoothly.
- Tip: Regularly check wires and connections to catch any signs of loosening or corrosion from vibration or weather.
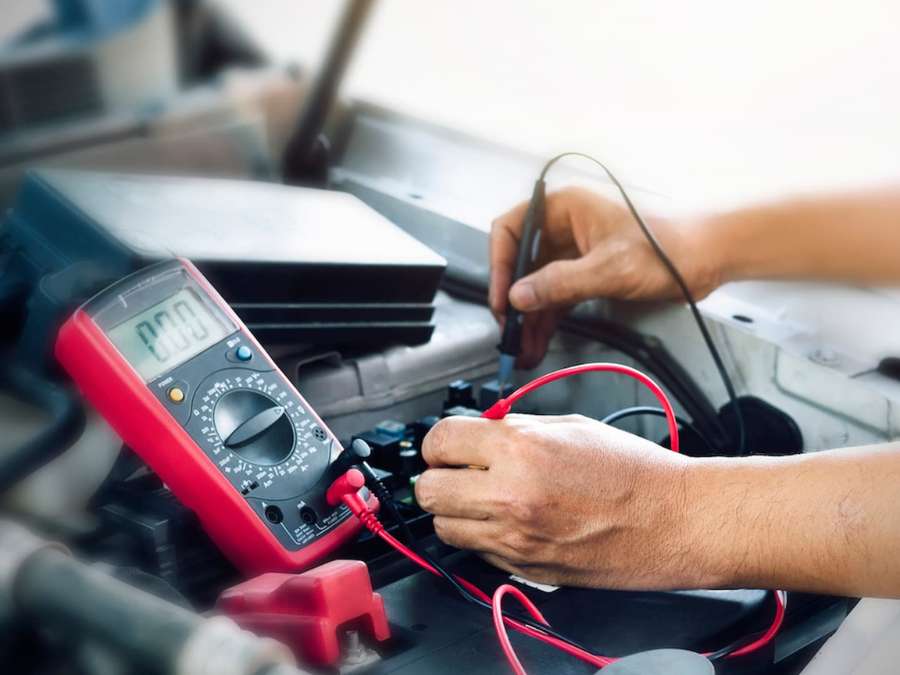
4. Worn Out Brushes
Brushes in the alternator are responsible for conducting electrical current. Over time, they wear down, leading to poor contact and reduced performance. Here are some reasons why brushes wear out quickly:
Friction Over Time
- Problem: Brushes wear down due to constant friction as they make contact with the alternator’s moving parts. This leads to poor conductivity.
- Solution: Replace brushes regularly to maintain proper contact and electrical flow.
- Tip: Keep track of brush lifespan and replace them before they get too short.
Overuse
- Problem: Running the alternator at high loads for long periods can cause the brushes to wear out faster than usual.
- Solution: Limit excessive use and give the alternator breaks to prevent overheating and excessive brush wear.
- Tip: Monitor the alternator’s workload and avoid pushing it to its limits for extended periods.
Poor Quality Brushes
- Problem: Low-quality brushes tend to wear out more quickly, leading to faster failure and more frequent replacements.
- Solution: Use high-quality replacement brushes that are designed for long-lasting performance.
- Tip: Choose reliable brushes from trusted suppliers like EPO, with 25 years of industry experience. This helps prevent premature wear and reduces the need for frequent replacements.
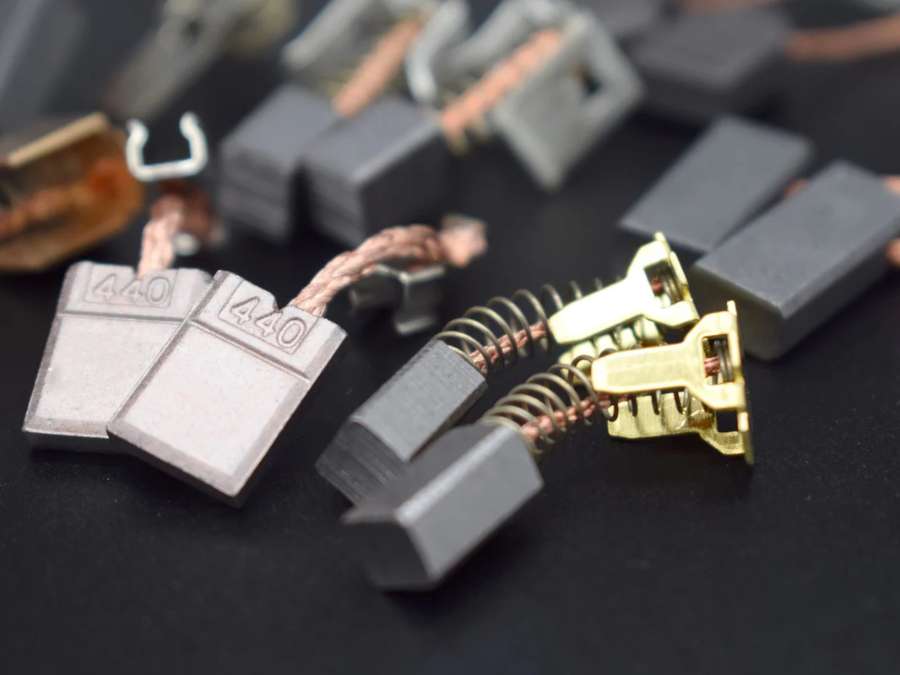
5. Excessive Heat
Excessive heat is one of the biggest threats to an alternator’s lifespan. High temperatures can damage critical parts, leading to failure. Here are some common reasons why this happens:
Poor Ventilation
- Problem: Without proper airflow, the alternator overheats, which can damage internal components over time.
- Solution: Keep cooling fans, vents, and air passages around the alternator clear to prevent heat buildup.
- Tip: Regularly check and clean cooling areas to avoid blocked airflow that can cause overheating.
Overworked Alternator
- Problem: Running the alternator under heavy loads for long periods can cause it to overheat, leading to damage.
- Solution: Allow breaks during heavy use to give the alternator time to cool down.
- Tip: Monitor workload levels and avoid running the alternator at its maximum capacity for extended periods.
High Ambient Temperatures
- Problem: Extremely hot environments add extra heat to the alternator, causing it to run hotter than normal.
- Solution: Operate machinery in shaded or cooler areas when possible to lower the surrounding temperature.
- Tip: Inspect the machine’s environment and consider adding external cooling if it frequently operates in hot conditions.
6. Loose or Worn Belt
The alternator’s belt drives its movement, and if it becomes loose or worn, the alternator won’t work efficiently. Here are common causes of belt issues:
Belt Stretching
- Problem: Over time, belts stretch, becoming loose and reducing tension. This can cause the alternator to slip and not charge properly.
- Solution: Regularly inspect and adjust the belt tension or replace stretched belts.
- Tip: Check belt tension during routine maintenance to catch signs of stretching early.
Cracking or Wear
- Problem: Belts can crack or wear down, leading to slippage or breakage, which disrupts the alternator’s function.
- Solution: Replace belts showing any signs of cracking or fraying to avoid sudden failure.
- Tip: Visually inspect belts for wear every few months, especially in high-use machinery.
Misalignment
- Problem: If the belt is misaligned, it causes uneven wear and increased friction, leading to faster deterioration.
- Solution: Align the belt properly during installation and check its alignment regularly.
- Tip: Keep an eye on belt alignment after repairs or maintenance to avoid uneven wear.
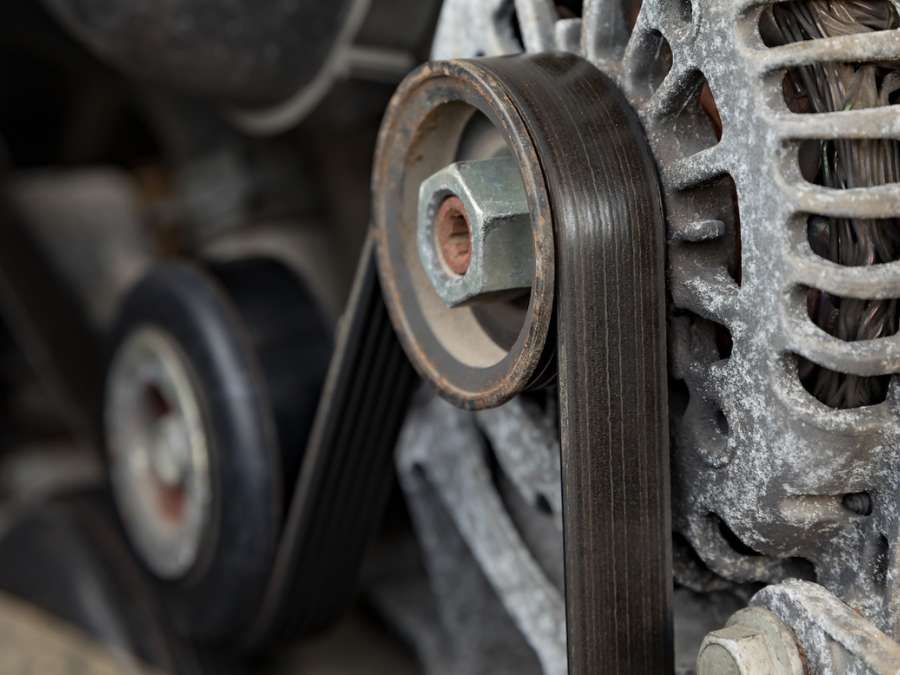
7. Electrical Overload
An electrical overload occurs when the alternator is asked to power more than it was designed to handle, leading to damage. Here’s why this happens:
Power Surges
- Problem: Sudden power surges can cause the alternator to overheat or short circuit, leading to failure.
- Solution: Install surge protectors to shield the alternator from unexpected spikes.
- Tip: Use protective equipment to guard against power surges, especially in areas prone to voltage fluctuations.
Incorrect Alternator Size
- Problem: Using an alternator that’s too small for the equipment’s power needs can lead to overload and failure.
- Solution: Always use an alternator sized correctly for the machinery it’s powering.
- Tip: Check your alternator’s specifications and match them to your machinery’s power requirements.
Short Circuits
- Problem: A short circuit in the system can cause electrical overload, damaging the alternator.
- Solution: Regularly inspect wiring to spot any shorts and fix them promptly.
- Tip: Routinely check wiring for any signs of wear or damage that might lead to a short circuit.
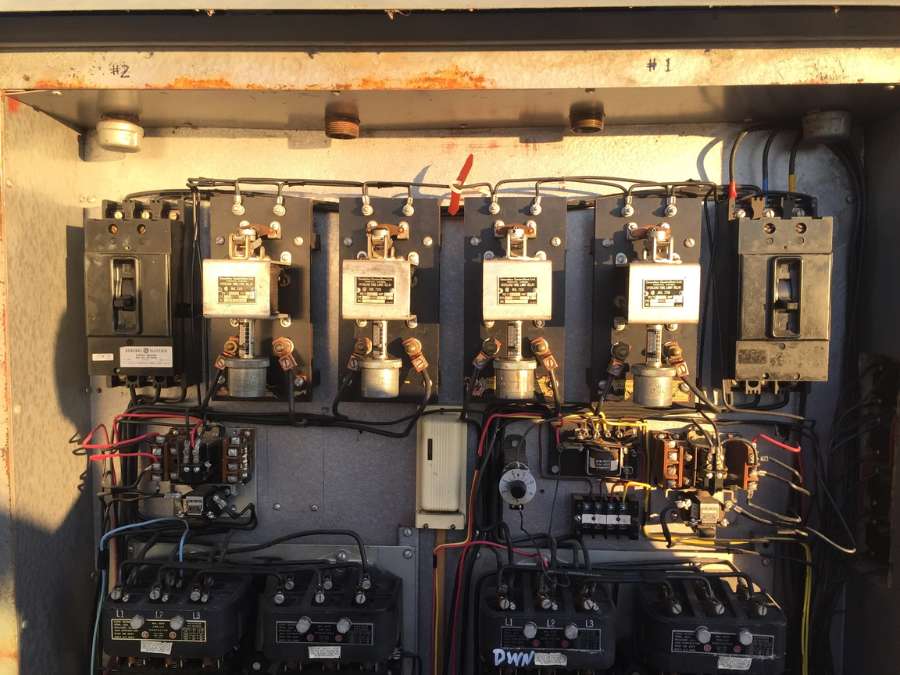
8. Damaged Wiring
Damaged wiring can interfere with the flow of electricity to and from the alternator, causing it to fail. Here are common causes:
Exposure to Heat
- Problem: Excessive heat can cause wires to melt or crack, leading to faulty connections.
- Solution: Use heat-resistant wiring and keep cables away from high-temperature areas.
- Tip: Regularly inspect wiring near hot engine parts to catch any heat damage before it spreads.
Vibration
- Problem: Constant vibration from machinery can loosen or damage wires, leading to shorts or disconnects.
- Solution: Secure wiring properly and use vibration-resistant materials in areas with high movement.
- Tip: Frequently check wires in high-vibration zones to ensure they’re secure and undamaged.
Corrosion
- Problem: Moisture or chemicals can corrode wiring over time, leading to poor connections or complete failure.
- Solution: Use corrosion-resistant materials and keep wiring dry and protected from chemicals.
- Tip: Inspect wires for signs of rust or corrosion regularly, especially in wet environments.
9. Leaking Fluids
Leaking fluids can seep into the alternator and damage its internal components, leading to failure. Here’s why it happens:
Oil Leaks
- Problem: Oil can leak into the alternator, damaging electrical components and reducing performance.
- Solution: Fix oil leaks immediately and keep the alternator area clean and dry.
- Tip: Regularly check the engine for oil leaks that could spill onto the alternator.
Coolant Leaks
- Problem: Coolant leaks can cause corrosion and short circuits inside the alternator, leading to damage.
- Solution: Repair any coolant leaks promptly to avoid fluid reaching the alternator.
- Tip: Inspect cooling systems and hoses regularly to prevent leaks near the alternator.
Power Steering Fluid Leaks
- Problem: Power steering fluid can leak onto the alternator, leading to electrical failure and damage.
- Solution: Check for power steering fluid leaks and keep the area around the alternator clean.
- Tip: Regularly inspect power steering systems for any signs of fluid leaks that could damage the alternator.
Water Intrusion
- Problem: Water from rain or cleaning can enter the alternator, causing electrical shorts or corrosion.
- Solution: Protect the alternator from water by covering it or using waterproof seals.
- Tip: Avoid using high-pressure water near the alternator when cleaning machinery.
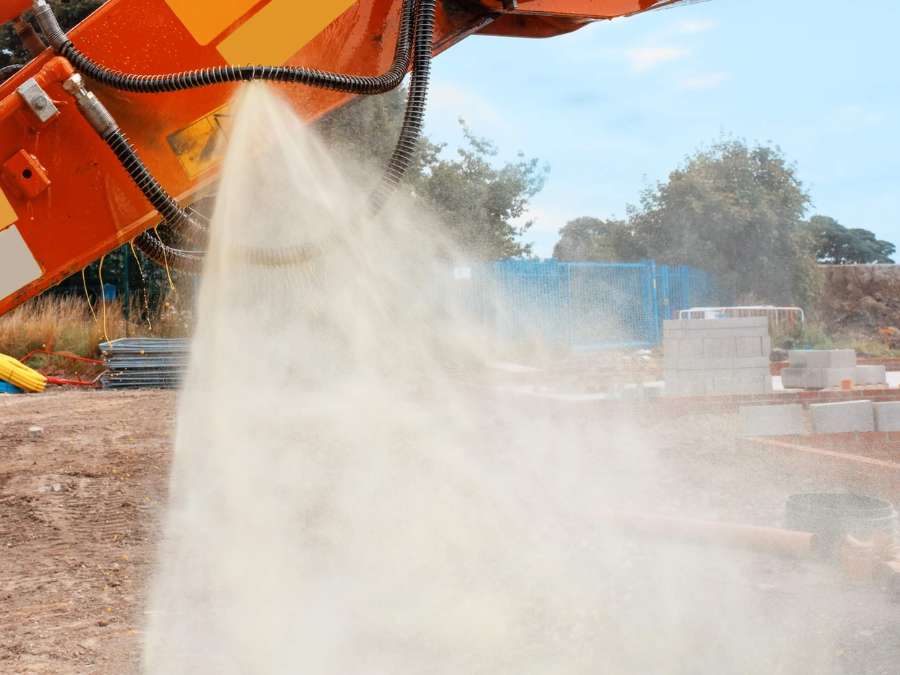
10. Faulty Diodes
Diodes inside the alternator convert AC to DC power. If they fail, the alternator stops charging properly. Here are common causes:
Age and Wear
- Problem: Over time, diodes wear out, causing the alternator to stop converting power effectively.
- Solution: Replace diodes as part of routine maintenance, especially in older alternators.
- Tip: Check diodes regularly if the alternator is more than a few years old.
Power Surges
- Problem: A sudden power surge can burn out diodes, leading to charging issues.
- Solution: Use surge protection devices to shield the alternator from electrical spikes.
- Tip: Install surge protectors if the machinery operates in areas prone to power fluctuations.
Poor-Quality Diodes
- Problem: Low-quality diodes may fail sooner, causing alternator malfunction and reduced lifespan.
- Solution: Use high-quality diodes designed to handle the alternator’s electrical load.
- Tip: Purchase diodes from trusted suppliers to avoid early failure.
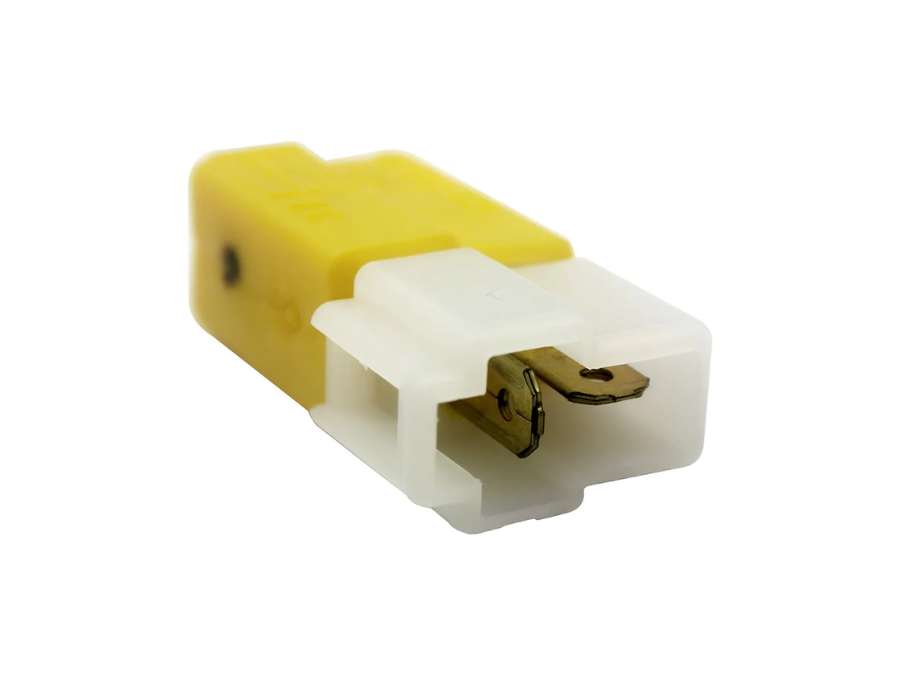
11. Excessive Alternator Load
Pushing the alternator beyond its design capacity can quickly cause failure. Here are the common causes:
High Electrical Demand
- Problem: Connecting more devices than the alternator can handle increases the load and causes overheating or failure.
- Solution: Limit the number of devices connected or upgrade to a higher-capacity alternator.
- Tip: Know the power requirements of all connected devices to avoid overloading the alternator.
Continuous Heavy Load
- Problem: Running the alternator at full capacity for long periods without breaks causes wear and overheating.
- Solution: Give the alternator rest periods during high-demand operations to prevent damage.
- Tip: Monitor the alternator’s temperature during heavy use and reduce load if it starts running hot.
Poor Alternator Sizing
- Problem: Installing an alternator that’s too small for the equipment’s needs will lead to overload and failure.
- Solution: Choose the right alternator size for the job to avoid pushing it beyond its limits.
- Tip: Consult a professional to confirm the right alternator size for your machinery. At EPO, our staff is trained to understand your specific needs, helping you choose the correct part without hassle.
Conclusion
Alternator failure can happen for many reasons. Knowing what causes these issues can help you spot problems early and keep your equipment running smoothly. Taking action before it’s too late can save you time and money.
In conclusion, this guide covers the top reasons why alternators fail and what you can do to prevent it. If you’re looking for a reliable partner for machinery parts, contact us today. We’re here to help you find the right solutions quickly and efficiently!