Are hydraulic oil leaks causing costly delays in your operations? These leaks can be a major issue, impacting equipment efficiency and leading to unexpected expenses.
As an excavator parts expert, I understand the complexities behind hydraulic oil leakage causes and how they can affect your machinery’s performance.
Here are 2 of the most common reasons behind hydraulic oil leaks that you need to be aware of:
- Worn Seals and Gaskets
- Loose or Damaged Fittings
In this guide, you’ll also discover other key causes of hydraulic oil leaks, along with actionable steps to prevent them and keep your machinery in top condition.
So let’s get started!
1. Quick Overview
Hydraulic oil leaks can lead to costly downtime and repairs if not dealt with right away. By identifying the common causes, you can prevent these problems and maintain smooth operation. Here’s a quick reference to the top 10 causes of hydraulic oil leakage:
Cause | Problem | Solution |
Worn Seals and Gaskets | Seals and gaskets wear out, leading to oil leaks. | Replace seals and gaskets with high-quality parts as soon as wear is detected. |
Loose or Damaged Fittings | Fittings loosen or get damaged, causing oil to leak. | Tighten loose fittings or replace damaged ones immediately. |
Cracked Hydraulic Hoses | Cracked hoses leak oil under pressure. | Replace cracked hoses and use pressure-rated hoses for your system. |
Excessive Pressure | High pressure damages seals and hoses, leading to leaks. | Adjust system pressure and install relief valves to manage excess pressure. |
Improper Installation | Incorrect installation causes loose or misaligned parts. | Follow proper installation procedures and check part alignment after installation. |
Corroded Components | Corrosion weakens parts, causing leaks. | Replace corroded parts and use corrosion-resistant materials like stainless steel. |
Oil Contamination | Contaminated oil wears out parts quickly. | Use high-quality filters, store oil properly, and regularly test oil for contaminants. |
Overfilled Reservoir | Too much oil causes pressure buildup and leaks. | Drain excess oil to keep levels within recommended limits. |
Thermal Expansion | Heat causes oil to expand, increasing pressure and leaks. | Use oil with appropriate temperature ratings and install heat exchangers if necessary. |
Vibration and Mechanical Stress | Vibration loosens fittings and damages components. | Use vibration dampeners and inspect components regularly for signs of stress. |
2. Worn Seals and Gaskets
Worn seals and gaskets often cause hydraulic oil leaks as they degrade over time, letting oil escape. Addressing these issues promptly is key to maintaining smooth operations. The demand for quality gaskets and seals reflects their importance in maintaining system efficiency; recent market analysis shows that the global gaskets and seals market is expected to grow to $89.9 billion by 2032.
- Cause: Over time, seals and gaskets can crack or become brittle due to constant pressure and temperature changes. This wear allows oil to escape, creating leaks that reduce the efficiency of your hydraulic system.
- Solution: Replace seals and gaskets as soon as you notice signs of wear, such as oil stains or drops around joints. Using high-quality replacements can help extend the life of these parts.
- Tips: Regularly inspect your seals and gaskets for early signs of wear, like small cracks or deformations. Keeping a maintenance schedule can help catch issues before they escalate, saving you time and money.
3. Loose or Damaged Fittings
Loose or damaged fittings can quickly lead to hydraulic oil leaks, causing messes and unexpected maintenance. Even a small gap in a fitting can allow oil to escape under pressure. Let’s look at the common causes, solutions, and practical tips to address this issue:
- Cause: Fittings connect different parts of the hydraulic system, keeping everything tight. When these fittings become loose or damaged, they no longer hold the pressure properly, allowing oil to leak out. For example, if you notice hydraulic fluid pooling under your excavator, it could be due to a loose fitting that has started leaking oil.
- Solution: Tighten loose fittings using the correct tools, being careful not to overtighten, which can damage the threads. Replace any damaged fittings immediately to prevent further leaks.
- Tips: Regularly check the tightness of fittings during routine maintenance and look for any signs of wear or damage. Use thread sealant where needed to help create a better seal, and always follow the manufacturer’s guidelines for torque specifications.
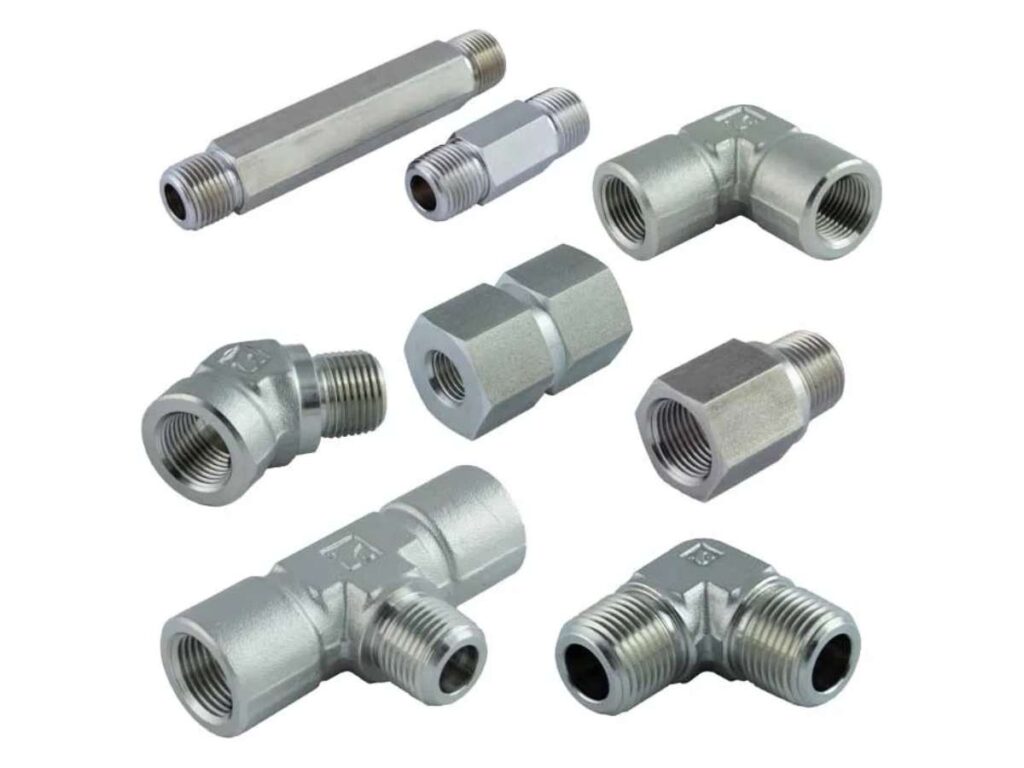
4. Cracked or Damaged Hydraulic Hoses
Cracked or damaged hydraulic hoses can cause significant oil leaks and lead to serious equipment downtime. Over time, exposure to harsh conditions can make hoses brittle and prone to cracks. Let’s dive into the common causes, solutions, and helpful tips to address this problem:
- Cause: Hydraulic hoses carry pressurized fluid throughout the system. When these hoses crack or get damaged, they can no longer handle the pressure, causing oil to leak out.
- Solution: Replace cracked or damaged hoses as soon as you notice signs of wear. Use hoses that match the right pressure rating and temperature range for your equipment to avoid future damage.
- Tips: Inspect hoses regularly for any signs of cracks, bulges, or leaks. Keep hoses clean and free of debris, as dirt can cause small abrasions over time. Store spare hoses properly to avoid kinking, which can weaken them before use.
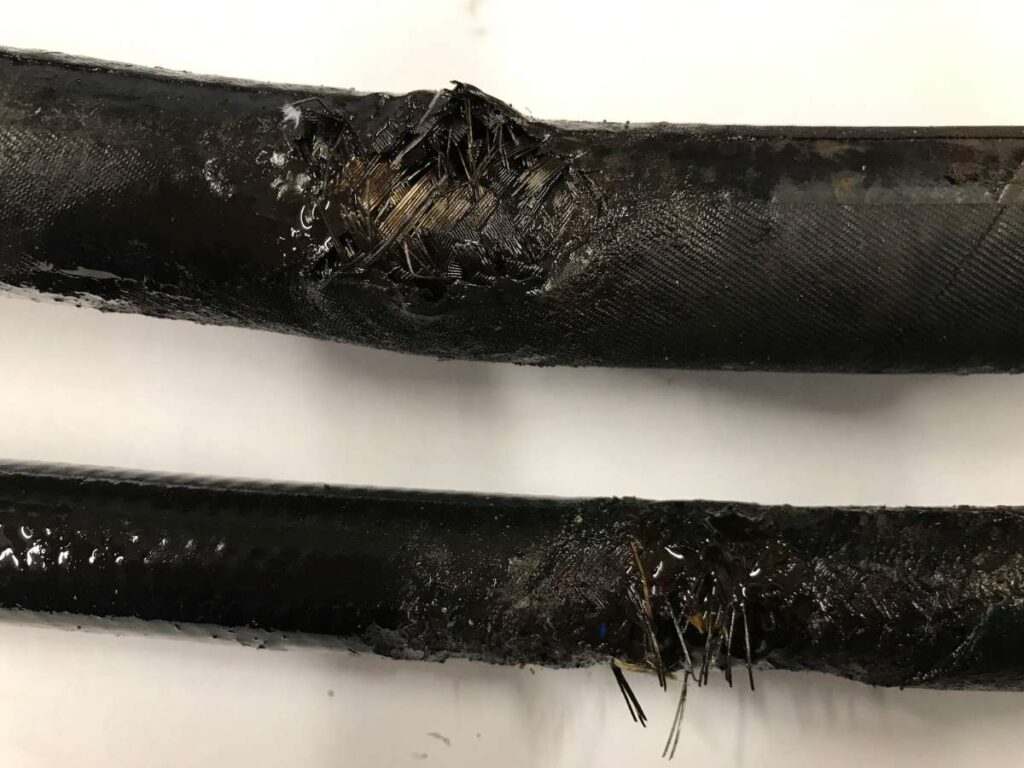
5. Excessive Pressure
Excessive pressure in a hydraulic system can lead to sudden leaks, causing damage to various components. It often happens when the system operates beyond its designed pressure limits. Below are the key causes, solutions, and tips to manage this problem effectively:
- Cause: When a hydraulic system faces pressure that’s too high, it can cause hoses, seals, and other components to burst or wear out faster. This can happen due to a faulty relief valve or incorrect settings in the system.
- Solution: Adjust the pressure settings to match the recommended levels for your equipment. Replace faulty relief valves and make sure all components are rated to handle the system’s pressure.
- Tips: Regularly monitor the pressure gauge to identify any unusual spikes or drops. At EPO, we manufacture high-quality excavator parts, including pressure relief valves designed to match your system’s capacity. Additionally, it’s important to watch for signs of wear caused by high pressure, such as bulging hoses or leaking seals.
6. Improper Installation
Improper installation of hydraulic components can lead to leaks and other issues that affect system performance. Even small mistakes during setup can create big problems down the line. Here’s a look at the common causes, solutions, and tips to fix this issue:
- Cause: When parts like hoses, fittings, or seals are not installed correctly, they might not align properly or create a secure connection. This can lead to loose connections and leaks that reduce system efficiency.
- Solution: Follow the manufacturer’s installation guidelines closely, using the right tools for each component. Double-check the alignment and tightness of parts to make sure everything fits together correctly.
- Tips: Train your team on proper installation techniques and keep detailed manuals on hand for reference. Conduct a quick test run after installation to spot any leaks or loose connections before putting the equipment into full use.
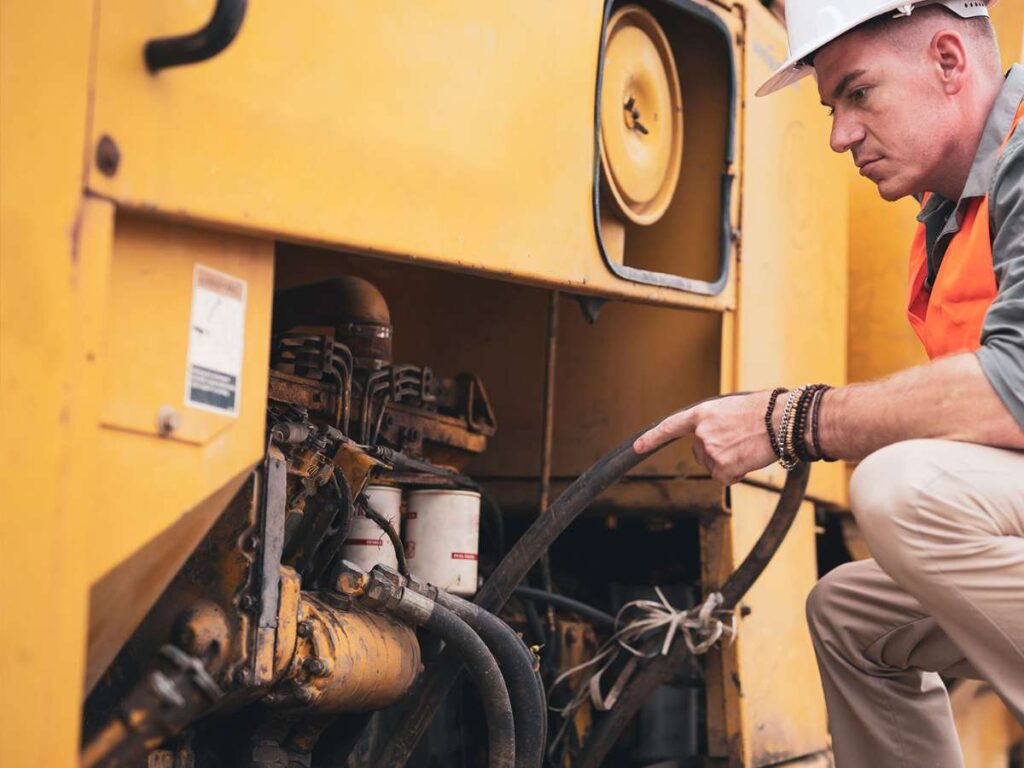
7. Corroded Components
Corroded components can cause hydraulic systems to weaken and leak over time. Exposure to moisture, chemicals, or harsh environments can speed up the corrosion process, leading to damaged parts. Below are the causes, solutions, and tips to tackle this problem:
- Cause: Corrosion happens when metal parts in the hydraulic system react with moisture or chemicals, breaking down the surface. This can lead to pitting, rust, and weakening of components, eventually causing leaks or even failure of the part.
- Solution: Replace any corroded components as soon as possible to prevent further damage. Use high-quality parts from EPO, made with corrosion-resistant materials like stainless steel, or apply protective coatings to keep moisture out.
- Tips: Keep hydraulic systems clean and dry, and store equipment in a controlled environment when not in use. Regularly check for signs of rust or discoloration on metal parts and take action early to avoid bigger issues.
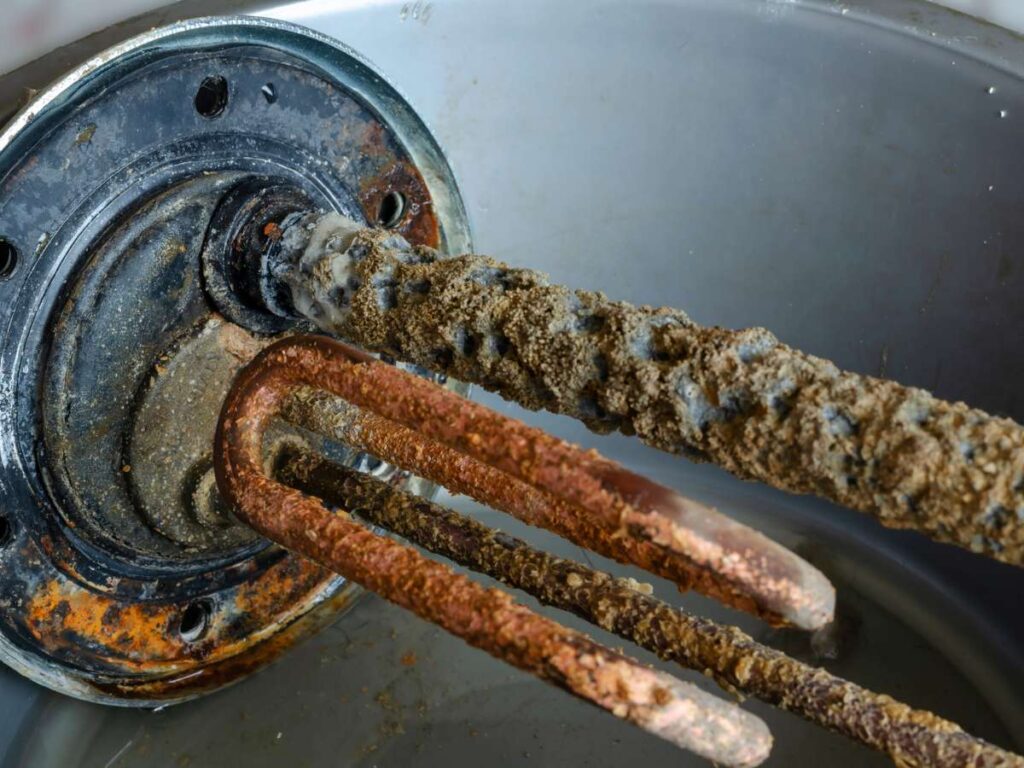
8. Oil Contamination
Oil contamination can quickly damage hydraulic systems, leading to wear and tear on critical components. Tiny particles, moisture, or other impurities in the oil can reduce the system’s efficiency and cause leaks. Here’s what you need to know about the causes, solutions, and tips for preventing oil contamination:
- Cause: Contaminants like dirt, water, or metal particles can enter the hydraulic system through improper storage, poor filtration, or leaks. These impurities mix with the oil, causing friction and damage to internal parts over time.
- Solution: Use high-quality filters and change them regularly to keep contaminants out of the oil. Make sure to store oil in clean, sealed containers and keep the system’s reservoir covered to prevent debris from entering.
- Tips: Perform regular oil analysis to catch contamination early and replace the oil when it shows signs of impurities. Train your team to handle oil carefully and keep the work area clean to avoid introducing dirt or water into the system.
9. Overfilled Reservoir
An overfilled reservoir can cause hydraulic systems to malfunction, leading to leaks and pressure issues. When there’s too much fluid, it can create excess pressure, which puts stress on seals and other components. Here’s a look at the causes, solutions, and tips to handle this situation:
- Cause: When too much oil is added to the reservoir, it can overflow or cause pressure to build up beyond the system’s capacity. This extra pressure can damage seals and lead to leaks. For example, if you notice oil leaking around the seals or spilling from the reservoir cap, it could be due to overfilling, which has caused excess pressure.
- Solution: Always fill the reservoir to the manufacturer’s recommended level. If overfilled, drain the excess oil immediately to bring it back within the proper range.
- Tips: Use a dipstick or level gauge to check the oil level before starting the equipment. Train staff to follow proper filling procedures, and mark the correct fill line on the reservoir to avoid overfilling.
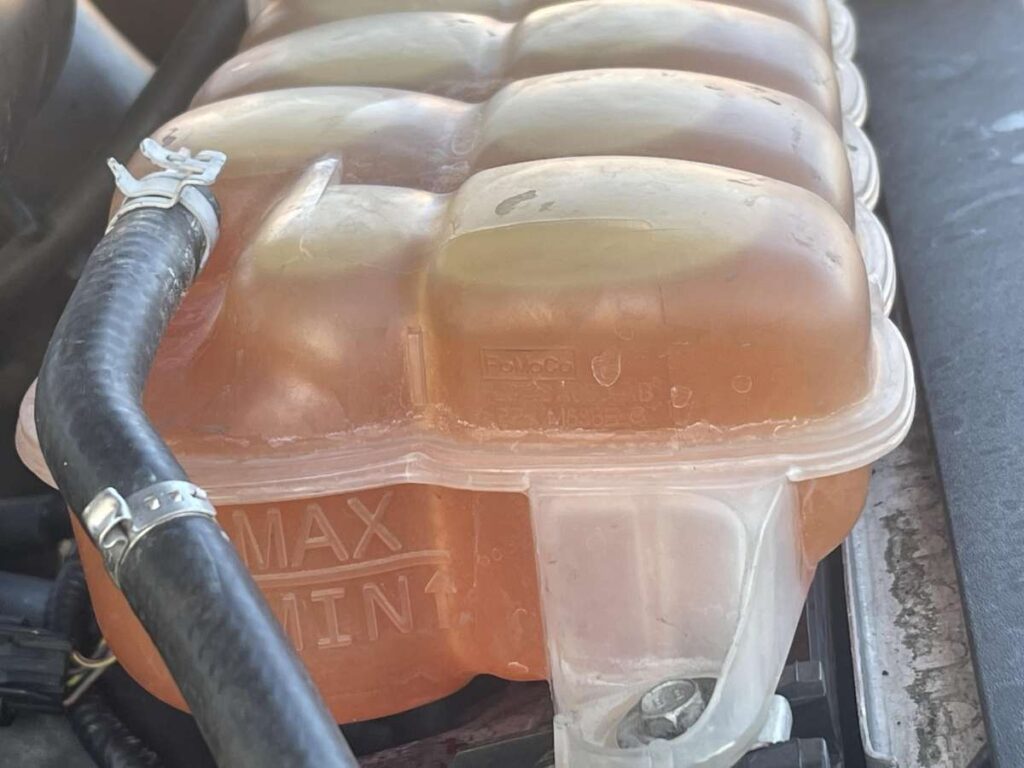
10. Thermal Expansion
Thermal expansion happens when the hydraulic fluid heats up and expands, putting extra pressure on the system. This increase in pressure can cause leaks and stress on seals and hoses. Here’s what you should know about the causes, solutions, and tips for managing thermal expansion:
- Cause: As hydraulic systems run, the fluid inside heats up, especially during long periods of use. When the fluid expands due to heat, it can create more pressure than the system is designed to handle, leading to leaks.
- Solution: Use oil with a suitable temperature range for your equipment and install a pressure relief valve to manage excess pressure from thermal expansion. Consider adding a heat exchanger to maintain the oil temperature within safe limits.
- Tips: Regularly monitor the temperature of your hydraulic system during operation. Avoid overworking the system for extended periods, and allow time for cooling if the temperature gets too high.
11. Vibration and Mechanical Stress
Vibration and mechanical stress can wear down hydraulic components over time, leading to leaks and damage. Constant shaking or physical strain can loosen fittings and weaken hoses. Here’s a closer look at the causes, solutions, and tips to manage this issue:
- Cause: When a hydraulic system experiences frequent vibration or mechanical stress, it can cause parts to loosen, crack, or wear out. This is common in equipment that operates on rough terrain or with heavy-duty tasks.
- Solution: Install vibration dampeners or use flexible hoses that can handle movement. Secure fittings tightly and use clamps to keep hoses in place, reducing the effects of vibration.
- Tips: Inspect the system regularly for signs of wear or loose parts. Make adjustments or repairs immediately when you notice any movement or abnormal noise during operation, and consider reinforcing high-stress areas with extra support.
Conclusion
Hydraulic oil leaks can cause serious issues for your equipment, leading to downtime and extra expenses. Understanding the common causes helps you take action before problems get worse. Addressing these issues quickly can keep your machinery running smoothly.
We hope this guide has helped you identify ways to address hydraulic oil leaks. At EPO, we know that waiting for quotes can be frustrating, which is why we provide same-day quotations along with high-quality, durable parts to solve these issues efficiently. Contact us today for fast, reliable solutions.