Are your excavators frequently breaking down, costing your business time and money? It’s frustrating when equipment fails, but understanding the common problems can help you tackle them more efficiently.
As an excavator parts expert, I specialize in helping businesses identify and solve these issues efficiently, so you can keep your machines running smoothly and your projects on track.
Let’s take a look at 2 of the most frequent problems you may encounter:
- Engine Starting Issues
- Hydraulic System Failures
In this guide, you’ll learn how to identify and address these issues, improving your machine’s reliability and reducing costly repairs.
So let’s get started
1. Quick Overview
Excavators often encounter various issues that can cause delays and expensive repairs if not dealt with quickly. Spotting these problems early helps keep your equipment functioning efficiently. Here’s a quick guide to the top 12 common excavator problems:
Problem | Cause | Solution |
Engine Starting Issues | Battery issues, damaged starter, or wiring faults. | Clean terminals, check battery voltage, replace faulty components. |
Hydraulic System Failures | Low fluid, worn seals, clogged filters. | Check fluid levels, replace seals, and clean filters. |
Overheating Engine | Coolant leaks, radiator clogs, or fan failure. | Refill coolant, clean radiator, and inspect fan. |
Track Movement Problems | Debris, worn tracks, or faulty tensioning. | Remove debris, adjust track tension, and replace worn tracks. |
Excavator Won’t Swing or Slow Swinging | Low hydraulic fluid or faulty swing motor. | Refill hydraulic fluid, clean or replace motor filters. |
Loss of Power | Clogged fuel filters, air filters, or fuel injectors. | Replace filters and inspect fuel injectors for blockages. |
Electrical System Malfunctions | Faulty wiring, dead batteries, or alternator failure. | Inspect wiring, replace batteries, check alternator. |
Excessive Smoke from Exhaust | Poor combustion, dirty fuel injectors, or oil leaks. | Clean fuel injectors, inspect for leaks, and replace oil seals. |
Hydraulic Cylinder Drifting | Worn seals or faulty control valve. | Replace cylinder seals, check valves, and correct any issues. |
Bucket or Arm Not Responding | Hydraulic fluid issues, air trapped in the system, or faulty control valves. | Bleed hydraulic system, inspect control valves, and replace damaged components. |
Unusual Noises | Loose parts, worn bearings, or hydraulic issues. | Tighten loose parts, replace worn bearings, and check hydraulic system. |
Fuel System Problems | Clogged filters, contaminated fuel, or leaking fuel lines. | Replace filters, use high-quality fuel, and inspect fuel lines for leaks. |
2. Engine Starting Issues
Excavators that don’t start can cause major delays on a project site. Whether it’s a cold morning or a busy day, engine issues can slow down business and increase costs. Let’s look at the most common reasons behind these problems and how to fix them:
- Cause: The most common cause is a weak battery or corroded battery terminals, preventing the engine from getting enough power to start. Another possible reason is a faulty starter motor, which can stop the engine from turning over.
- Solution: Check the battery first. Clean the terminals and test the voltage to see if it needs replacing. If you need a new battery, EPO offers high-quality batteries specifically designed for excavators, providing dependable performance. If the battery is fine, inspect the starter motor and wiring for damage or loose connections. If these parts are worn out, you’ll need to replace them.
- Tips: To keep your excavator running smoothly, make it a habit to inspect the battery and fuel system weekly. Store the machine in a controlled environment during colder months to avoid start-up issues. Keeping spare parts like filters on hand can also prevent unexpected downtime.
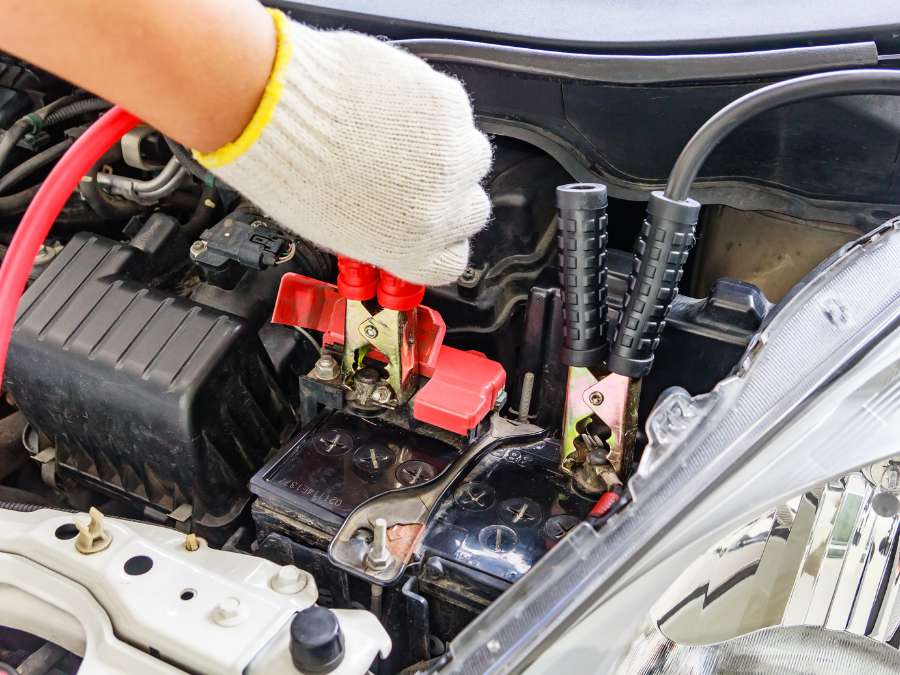
3. Hydraulic System Failures
Hydraulic systems are crucial for the smooth operation of your excavator, driving everything from the arm to the tracks. When the system fails, it can cause serious downtime and affect your project timelines. Here are some of the most common causes of hydraulic system failures and how to address them:
- Cause: Hydraulic system failures typically happen due to low fluid levels, contaminated oil, or worn-out seals. Leaks or blockages in the system can also cause machinery to lose power or perform inefficiently.
- Solution: Start by checking the hydraulic fluid levels and inspect for any leaks in hoses or seals. Replace worn-out seals and filter the oil to remove contaminants. Regularly maintaining the system and using high-quality hydraulic oil helps reduce the chance of future breakdowns.
- Tips: Inspect the hydraulic hoses and connections every week for wear and leaks. Keep the hydraulic fluid clean and at the right level to prevent costly repairs. Stock extra hoses and filters so you’re prepared for any emergency repairs.
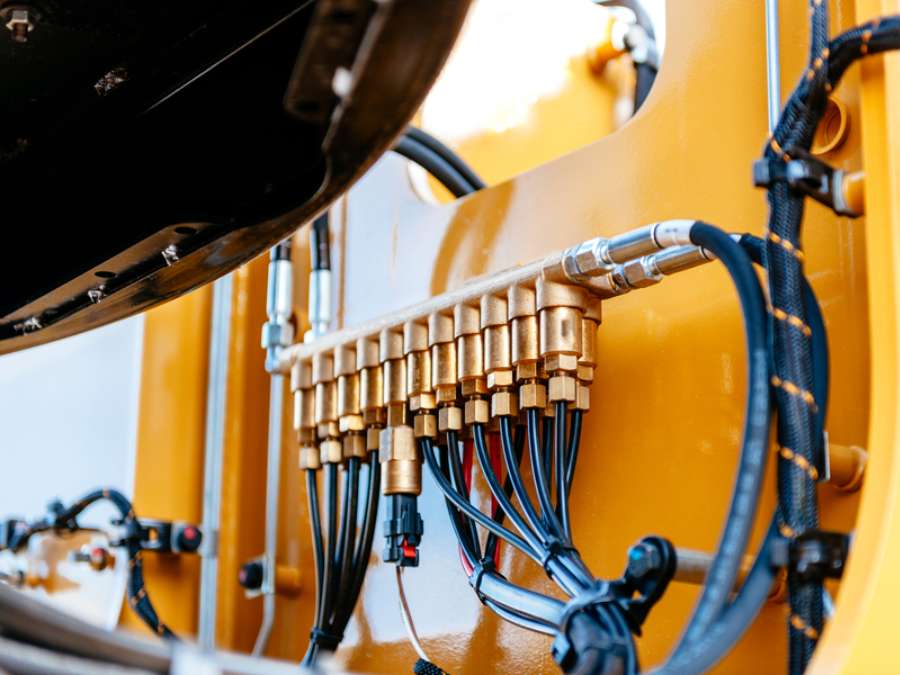
4. Overheating Engine
An overheating engine can stop your excavator in its tracks, leading to unplanned downtime and expensive repairs. Understanding what causes overheating and how to prevent it will keep your machine working smoothly. Let’s look at some common causes of engine overheating and how you can fix them:
- Cause: Engines usually overheat due to low coolant levels, a faulty radiator, or clogged filters. Dirt and debris can block airflow, preventing the engine from cooling properly, while leaks in the cooling system make things worse.
- Solution: Check the coolant level and top it off if needed. Clean or replace air filters, and inspect the radiator for any clogs or leaks. Keeping the cooling system well-maintained helps prevent overheating.
- Tips: Perform regular checks on your coolant levels and inspect the radiator and cooling system for leaks or blockages weekly. Clean the air filters to allow proper airflow, especially if you’re working in dusty conditions.
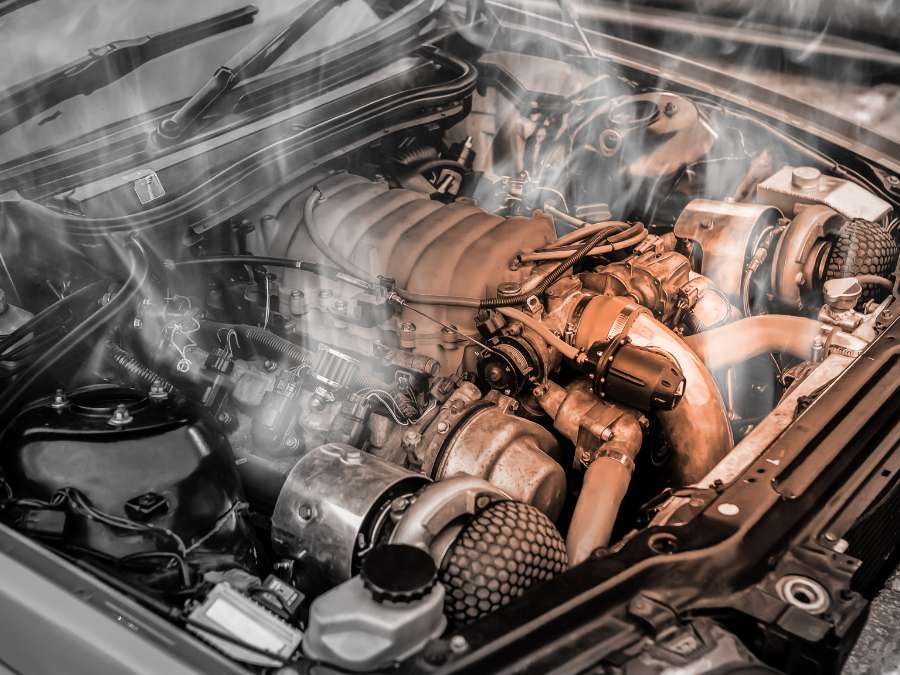
5. Track Movement Problems
If your excavator’s tracks aren’t moving smoothly or are getting stuck, it can severely impact your work efficiency. Fixing track issues early helps avoid more serious damage and delays. Here’s what you need to know to diagnose and fix track movement problems:
- Cause: Track movement issues often result from debris buildup, worn-out track chains, or a faulty tensioning system. Misaligned or damaged tracks can also cause uneven movement, making the excavator harder to control.
- Solution: Clear out any debris around the tracks, and check the track tension. If the tracks are loose or worn, adjust the tension or replace the chains. Keeping the tracks clean and aligned will help ensure smooth movement.
- Tips: Inspect the tracks daily, especially after working in muddy or rough conditions. Regularly clean out dirt and debris, and always check the tension. Tighten or loosen as necessary to prevent uneven wear and extend the life of your tracks.
6. Excavator Won’t Swing or Slow Swinging
If your excavator is struggling to swing or move slower than usual, it can slow down your entire operation. Getting to the bottom of the issue quickly will help you keep your project on track. Let’s break down the most common causes and solutions for swing issues:
- Cause: Swinging problems usually come from low hydraulic fluid levels, a clogged swing motor filter, or damaged swing gears. Sometimes, the issue is linked to faulty valves that control the swing function. For example, if you notice the excavator swinging unevenly or hesitating during movement, the hydraulic fluid may be low or the filter clogged.
- Solution: First, check the hydraulic fluid level and refill if it’s low. Clean or replace the swing motor filter, and inspect the swing gears for wear and tear. If the problem persists, check the valves and replace them if necessary.
- Tips: Make it a habit to check the hydraulic fluid levels and swing motor filter regularly. Keep an eye on the swing gears for early signs of damage. A little preventive maintenance goes a long way in avoiding costly repairs.
7. Loss of Power
When your excavator starts losing power, it affects productivity and can lead to bigger mechanical problems if not addressed quickly. Understanding the root cause will help you get the machine back to full strength. Here’s a look at why your excavator might be losing power and how you can solve it:
- Cause: Loss of power usually stems from clogged fuel filters, air filter issues, or problems with fuel injectors. If the engine isn’t getting the right fuel or airflow, it can’t run at full capacity.
- Solution: Start by checking the fuel and air filters. Replace any that are clogged or dirty, and inspect the fuel injectors for blockages. Keeping these components clean ensures a smooth and efficient fuel delivery system.
- Tips: Regularly change fuel and air filters to maintain consistent engine power. If you notice any hesitation or slowdowns, inspect the fuel injectors as early action can prevent more serious engine damage.
8. Electrical System Malfunctions
Electrical issues in your excavator can be tricky to diagnose, but they often result in operational delays or safety concerns. Addressing electrical malfunctions promptly keeps your machines running smoothly and safely. Here are some typical electrical problems and how to resolve them:
- Cause: Electrical malfunctions usually occur due to faulty wiring, dead batteries, or failing alternators. Loose connections and worn-out fuses can also cause systems to malfunction, making it hard for the excavator to start or operate properly.
- Solution: Inspect the wiring for any damage or loose connections, and replace dead batteries or malfunctioning alternators. If you need a replacement, EPO offers high-quality alternators specifically designed for excavators, providing durable and reliable performance. Afterward, check that all fuses are intact, and if something seems off, it may be time to replace worn parts.
- Tips: Perform regular electrical system checks, especially on wiring and battery connections. Replace fuses and batteries as needed to prevent sudden failures, and always carry spare electrical parts for emergencies.

9. Excessive Smoke from Exhaust
When your excavator starts emitting too much smoke, it’s a sign that something is wrong with the engine. The type and color of smoke can help point you to the root of the problem. Let’s explore the common causes of excessive smoke and how to handle them:
Cause: Excessive smoke is often caused by burning oil, incomplete combustion, or fuel system problems. Black smoke may indicate too much fuel, while blue or white smoke could signal oil burning or coolant leakage.
Solution: Check the air filters and fuel injectors first, as blockages can disrupt proper combustion. If the smoke is blue or white, inspect the engine for oil leaks or coolant issues. Repair any leaks and replace faulty injectors as needed.
Tips: Regular maintenance of air filters and fuel injectors helps reduce the chance of smoke. Keep an eye on oil and coolant levels to catch any leaks before they turn into bigger problems.
10. Hydraulic Cylinder Drifting
Hydraulic cylinder drifting can cause your excavator’s attachments to shift or lose position, leading to delays and precision issues. Addressing this problem quickly is essential for maintaining smooth operations. Given the importance of hydraulic systems, the hydraulic cylinder market was expected to grow at a 4.2% CAGR through 2030, highlighting the need to keep these systems in top condition according to Grand View Research.
When a hydraulic cylinder drifts, it can cause your excavator’s attachments to slowly move or lose position, leading to precision issues and operational delays. Tackling this problem quickly will prevent further complications. Here’s a breakdown of the causes and how to fix hydraulic cylinder drifting:
- Cause: Hydraulic cylinder drifting usually happens due to internal leaks in the cylinder seals or a faulty control valve. When the seals wear down, oil bypasses the piston, causing the cylinder to move unintentionally. For example, if you notice the excavator’s arm lowering on its own while at rest, this is a sign of cylinder drifting caused by worn seals.
- Solution: Inspect the cylinder seals for wear and replace them if necessary. Check the control valve to make sure it’s functioning properly. Replacing damaged seals and addressing valve issues will stop the drifting.
- Tips: Perform regular checks on cylinder seals and control valves to spot wear early. Replacing seals as soon as you notice drifting will save you from bigger repairs later on. Keep spare seals and a basic repair kit on-site to handle the problem quickly.
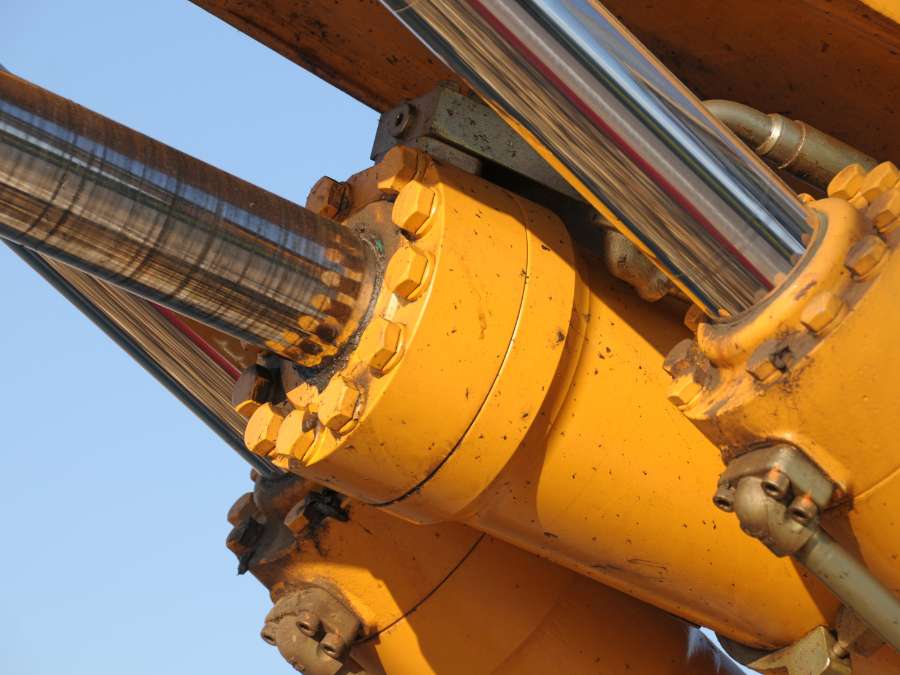
11. Bucket or Arm Not Responding
When the bucket or arm of your excavator stops responding, it can cause serious delays, making it difficult to complete tasks on time. Quickly identifying the cause will help you get back to work without major setbacks. Let’s dive into why this issue occurs and how to fix it:
- Cause: A non-responsive bucket or arm is often caused by hydraulic fluid issues, such as low fluid levels, air trapped in the system, or clogged filters. Faulty control valves or damaged hydraulic lines can also be responsible for this malfunction.
- Solution: Start by checking the hydraulic fluid level and looking for any trapped air in the system. Bleed the hydraulic lines to remove air bubbles, and inspect the control valves and filters for any blockages. Fixing these areas will restore proper movement.
- Tips: Monitor your hydraulic fluid levels regularly and replace filters before they become clogged. If you notice sluggish movements or delayed responses, bleed the lines as a preventative measure. Having spare control valves and filters on hand can help reduce downtime.
12. Unusual Noises
Strange noises coming from your excavator are often a warning sign that something is wrong. Ignoring these sounds can lead to more significant issues down the line, so it’s important to identify the cause early. Let’s take a closer look at common causes and how to address them:
- Cause: Unusual noises typically come from loose parts, worn bearings, or issues within the hydraulic system. Grinding, squeaking, or knocking sounds often indicate parts that need lubrication or replacement.
- Solution: Inspect your machine for any loose bolts or components and tighten them as needed. Lubricate the moving parts regularly, and replace worn-out bearings to stop grinding or knocking sounds. Checking the hydraulic system for leaks or blockages can also help reduce noise.
- Tips: Listen closely to your excavator during operation to catch early signs of trouble. Perform routine checks on bearings and moving parts, lubricating them as part of your regular maintenance. Keeping spare bearings and lubrication on-site will help you stay ahead of any noise-related issues.
13. Fuel System Problems
Fuel system issues can cause your excavator to run inefficiently or even stall completely. Identifying the problem early can save you from costly repairs and downtime on the job site. Here’s how to diagnose and fix common fuel system issues:
- Cause: Fuel system problems often stem from clogged fuel filters, contaminated fuel, or air trapped in the fuel lines. These issues can block the flow of fuel, causing the engine to perform poorly or not run at all.
- Solution: Start by checking the fuel filter and replace it if it’s dirty or clogged. Inspect the fuel lines for air pockets, and bleed the system to remove trapped air. Using clean, high-quality fuel will also prevent contaminants from causing problems in the future.
- Tips: Replace your fuel filter regularly to keep the system running smoothly. Check the fuel lines for any leaks or air pockets and bleed the system if necessary. Keep extra filters and fuel line repair tools on hand to prevent extended downtime.
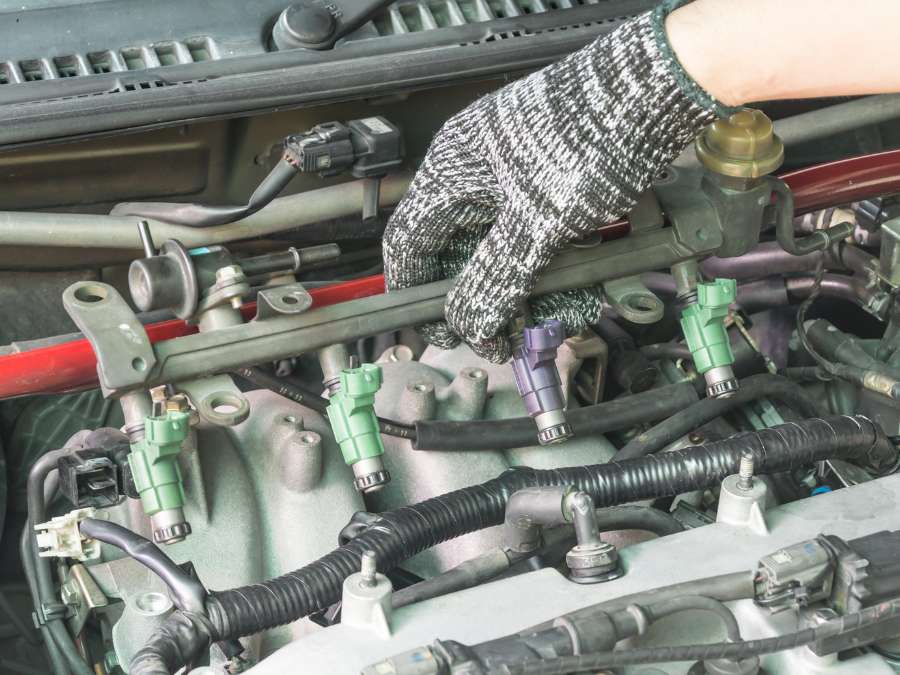
Conclusion
Dealing with excavator issues can be frustrating, but identifying the problem early can save you both time and money. From engine troubles to hydraulic failures, knowing what to look for helps keep your machine running smoothly. Regular maintenance and quick fixes can prevent bigger headaches down the road.
We hope this guide helps you address issues before they escalate. A common complaint in the industry is slow quotations, but EPO solves this with fast, same-day quotes. With 25 years of experience, we’re here to keep your machines running—contact us today for more information!