Which parts make your excavator bucket more durable and efficient? Understanding the key components of an excavator bucket can help you make smarter buying decisions and ensure your machinery operates smoothly.
As an excavator expert, I understand the importance of knowing each part of your bucket. Whether you’re managing a construction business or a repair shop, knowing the names and functions of these parts is crucial to your success.
Here’s a quick look at 2 essential parts of the excavator bucket:
- Bucket Teeth
- Cutting Edge
In this guide, we will discuss the remaining parts of the excavator bucket, their functions, and how they impact your equipment’s productivity.
So let’s get started!
1. Quick Overview
Excavator bucket parts are essential for maintaining efficient digging operations and preventing equipment damage. Each part serves a specific role in enhancing the bucket’s performance and durability. Here’s a quick overview of key excavator bucket parts and their functions:
Bucket Part | Function |
Bucket Teeth | Penetrates hard surfaces and breaks up materials. |
Cutting Edge | Slices through soil for efficient scooping. |
Side Cutters | Protects bucket sides while widening the cut. |
Bucket Lip | Provides structural support for the cutting edge and teeth. |
Wear Plates | Protects high-wear areas to extend bucket life. |
Shroud | Shields edges from impact and wear. |
Hinge Plate | Connects bucket to excavator arm, enabling movement. |
Pin Bosses | Secures pins that hold the bucket in place. |
Bucket Linkage | Transfers hydraulic power for controlled movement. |
Bottom Plate | Bears the ground contact during excavation. |
Side Plates | Reinforces the bucket sides for durability. |
Back Plate | Provides rear stability for the bucket. |
Heel Shrouds | Protects the rear corners from wear during digging. |
Understanding excavator bucket parts is key to maintaining your equipment’s efficiency and performance. Each part has a specific function that contributes to better digging and smoother operations. If you’re looking for high-quality parts at competitive prices, EPO offers durable, reliable solutions to keep your machines running efficiently. Contact us today to learn more!
2. Bucket Teeth
Bucket teeth are the pointed components located at the front of an excavator’s bucket. They are essential for digging and breaking through tough materials like soil, rock, and gravel. These teeth are made from durable metals, designed to withstand constant wear and tear in demanding environments.
Specifications
- Material: High-strength steel with heat-treated alloy
- Hardness: 500 Brinell for superior durability
- Mounting Style: Pin-on or weld-on attachment
- Weight: 3-10 kg depending on size
- Length: 8-12 inches based on application
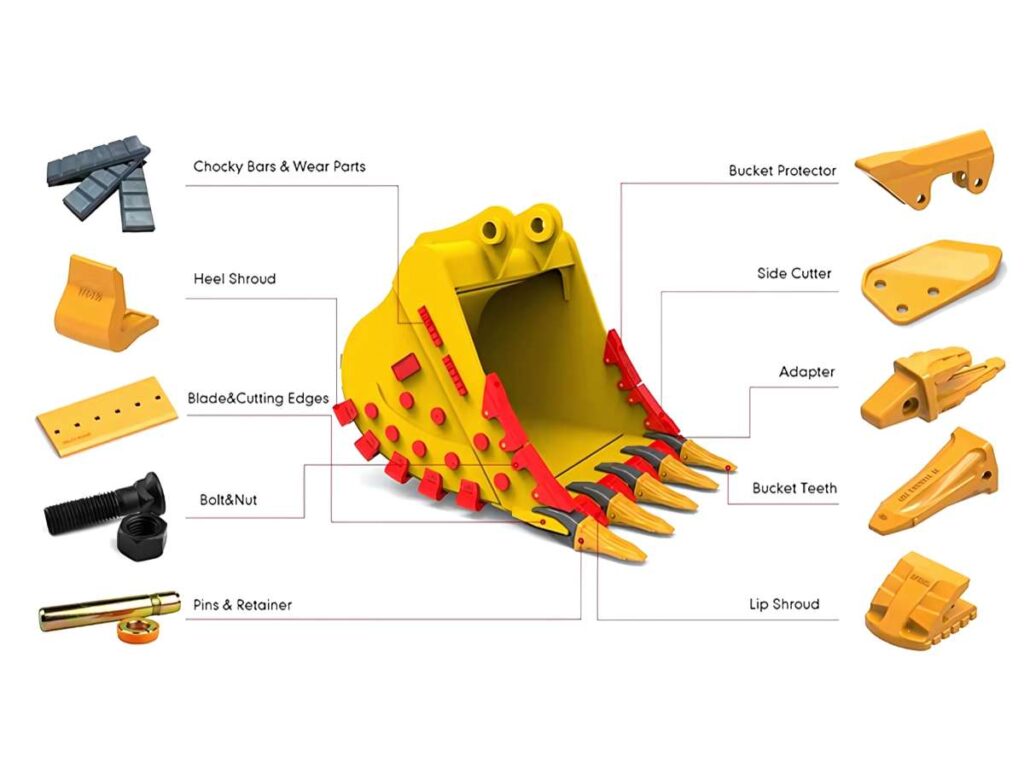
The main function of bucket teeth is to break through hard ground and carry materials into the bucket. They improve the digging capability of the excavator, allowing it to work faster and more efficiently. Without strong bucket teeth, the machine would struggle to dig into harder surfaces, resulting in slower progress and higher operational costs.
3. Cutting Edge
The cutting edge is a long, flat blade located at the front lip of the excavator bucket. It helps slice through materials like soil, sand, and gravel, making it easier for the bucket to scoop them up. Built from strong, wear-resistant steel, the cutting edge is designed to handle heavy use without wearing down quickly.
Specifications
- Material: High-carbon steel or abrasion-resistant alloy
- Thickness: Typically 1-3 inches
- Width: 4-10 inches depending on bucket size
- Length: Matches the width of the bucket, ranging from 36-72 inches
- Mounting Style: Bolt-on or weld-on options
The cutting edge helps the bucket penetrate the ground smoothly and improves its ability to scoop and load materials efficiently. It works by creating a clean slice through the material, reducing resistance and wear on the bucket itself. Without a sharp, durable cutting edge, digging operations would be slower, and the bucket would experience more wear and tear over time.
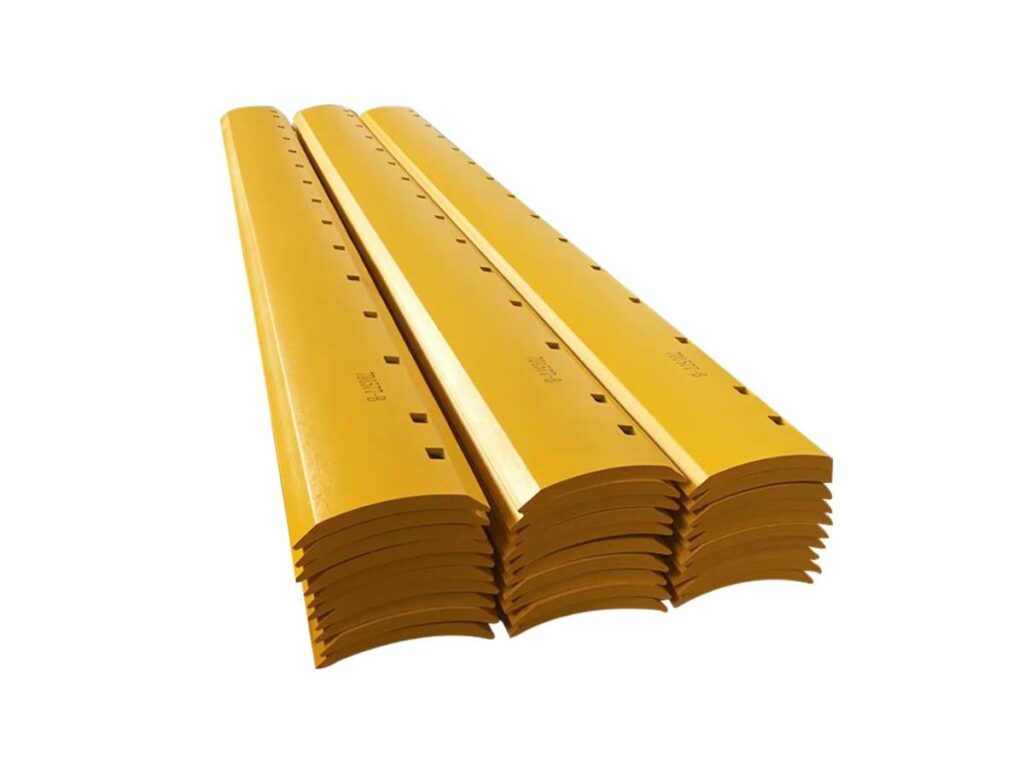
4. Side Cutters
Side cutters are additional cutting components mounted on the sides of the excavator bucket. They help protect the bucket’s sides while improving its ability to cut through dense materials during digging operations.
Specifications
- Material: Hardened steel or alloy steel
- Thickness: 1-2 inches
- Weight: 5-15 kg depending on size
- Mounting Style: Bolt-on or weld-on
- Compatibility: Varies based on bucket width and excavator model
Side cutters provide extra cutting power on the sides of the bucket, allowing for a smoother and wider excavation. They help reduce wear on the bucket’s sidewalls and increase overall digging efficiency, especially when working with dense or compacted materials. By widening the cut, side cutters also allow the bucket to hold more material per scoop, improving productivity.
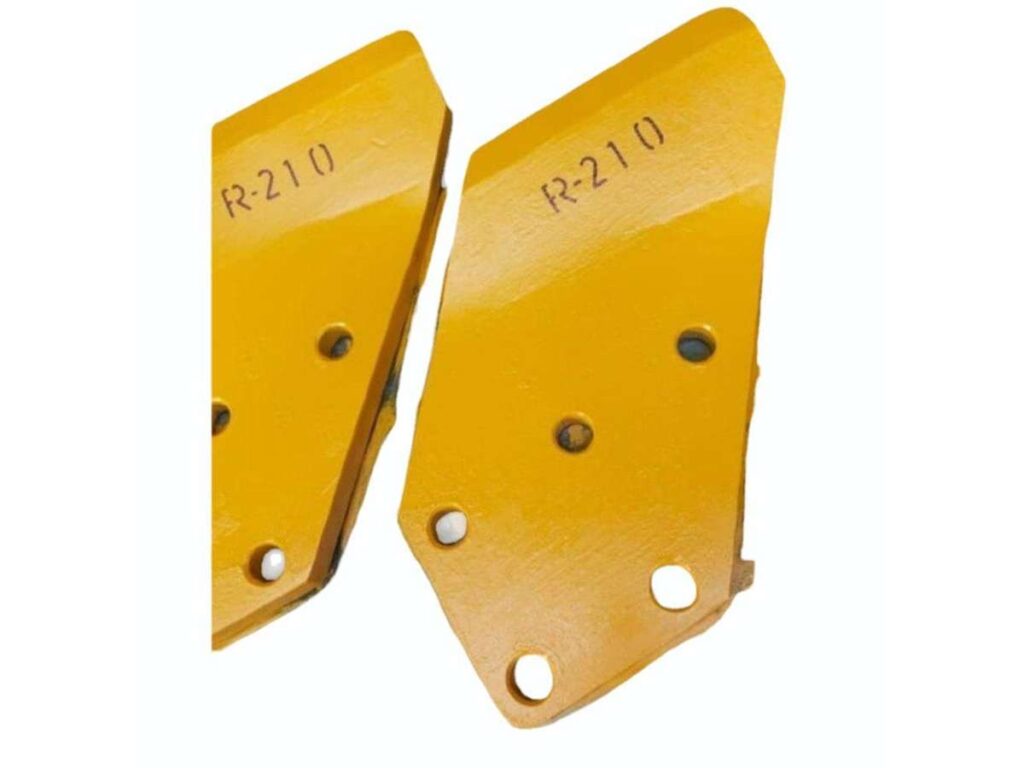
5. Bucket Lip
The bucket lip is the front edge of the bucket where the cutting edge and teeth are attached. It provides the foundation for these parts and helps keep the bucket structure strong during heavy digging operations.
Specifications
- Material: High-carbon steel or abrasion-resistant alloy
- Thickness: Typically 2-4 inches
- Length: Matches the width of the bucket (36-72 inches)
- Mounting Style: Welded or bolted to the bucket
The bucket lip plays a critical role in supporting the cutting edge and teeth, ensuring they remain securely in place while digging through hard surfaces. It also helps to evenly distribute the stress and pressure on the bucket during excavation, preventing damage to the overall structure of the bucket. Without a strong bucket lip, the teeth and cutting edge could wear out or become damaged more quickly.
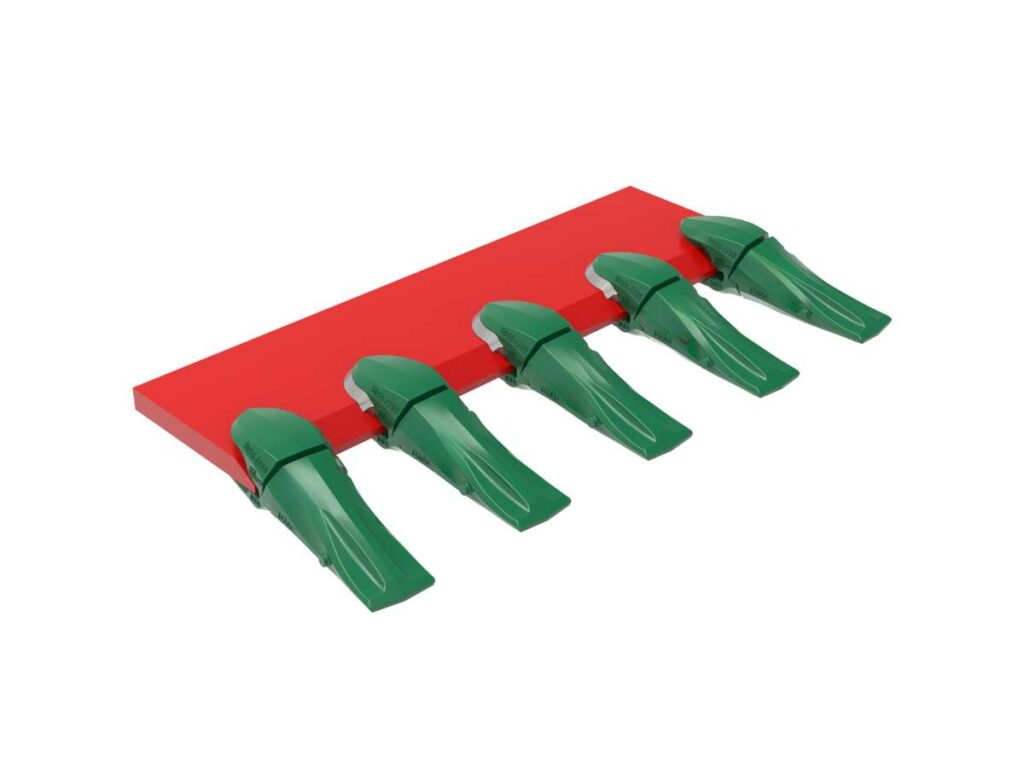
6. Wear Plates
Wear plates are protective steel plates attached to high-contact areas of the bucket. They prevent excessive wear on the bucket by absorbing the impact and friction that occurs during digging operations.
Specifications
- Material: Hardened steel or abrasion-resistant alloy
- Thickness: Typically 1-3 inches
- Length: Varies depending on bucket size, usually 12-36 inches
- Mounting Style: Weld-on
Wear plates are designed to protect the bucket’s structure from the constant scraping, impact, and friction that happens while digging. They extend the lifespan of the bucket by absorbing wear that would otherwise damage the bucket itself. This protection reduces maintenance costs and keeps the bucket performing at its best for longer periods.
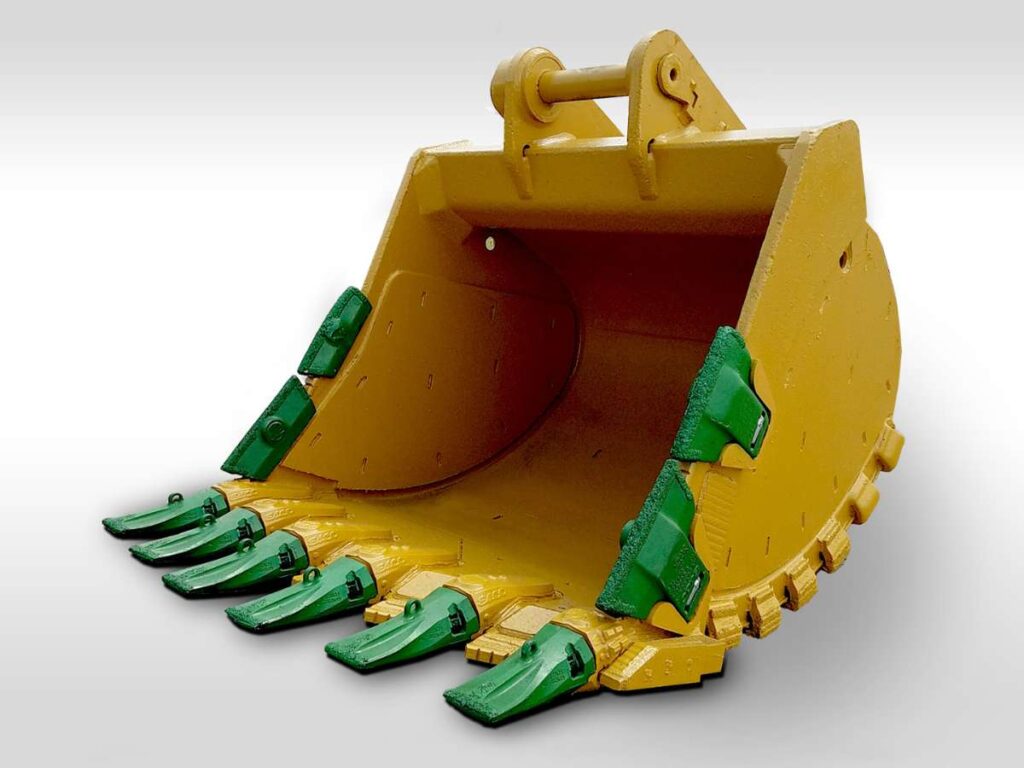
7. Shroud
A shroud is a protective cover installed on the bucket’s edges or other high-wear areas. It acts as an additional layer of protection to reduce damage from impacts and abrasion, especially when working with tough materials like rock or gravel.
Specifications
- Material: Hardened steel or wear-resistant alloy
- Thickness: Typically 1-2 inches
- Weight: 3-8 kg depending on size
- Mounting Style: Weld-on or bolt-on
The main function of the shroud is to protect vulnerable areas of the bucket, such as the sides and edges, from excessive wear. It absorbs the force of impacts, reducing the strain on the bucket and extending its operational life. This helps minimize downtime for repairs, allowing the machine to keep working efficiently.
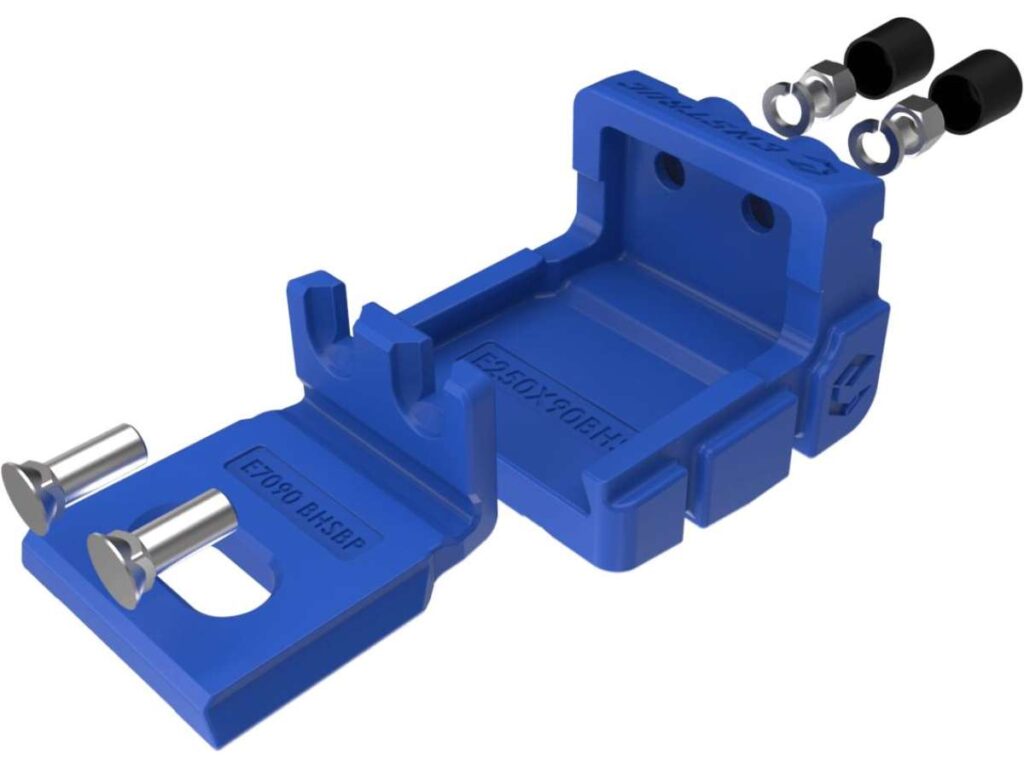
8. Hinge Plate
The hinge plate is the part of the bucket that connects it to the excavator arm, allowing the bucket to pivot during digging and dumping. It is a strong, reinforced plate designed to handle the constant movement and stress of the bucket’s operation.
Specifications
- Material: High-strength steel
- Thickness: Typically 2-4 inches
- Width: Varies based on bucket size, usually 12-24 inches
- Mounting Style: Welded directly onto the bucket
The hinge plate’s function is to provide a secure point of attachment between the excavator arm and the bucket, enabling smooth movement during digging and material unloading. It bears the weight of the bucket and the load, ensuring consistent performance during excavation tasks without causing excessive wear to the bucket’s structure.
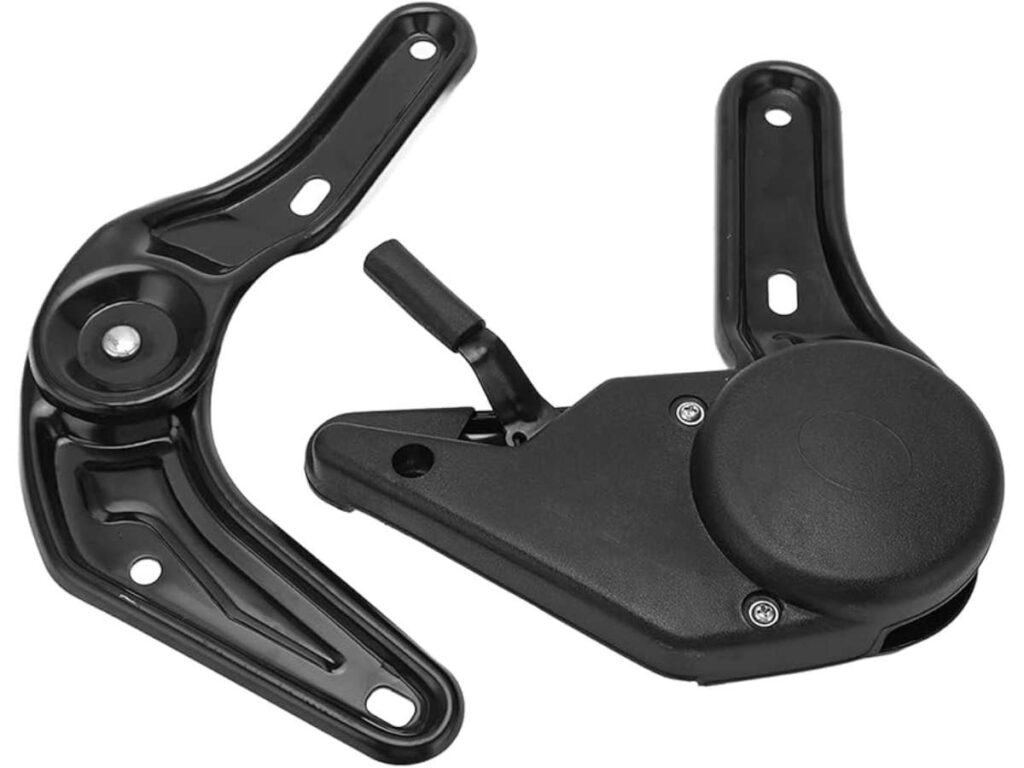
9. Pin Bosses
Pin bosses are reinforced sleeves or housings that hold the bucket’s pins in place. These pins connect the bucket to the excavator arm and help facilitate smooth pivoting during digging and material handling.
Specifications
- Material: Hardened steel or cast iron
- Inner Diameter: 2-4 inches, based on pin size
- Length: 3-8 inches depending on bucket design
- Mounting Style: Welded onto the bucket frame
Pin bosses provide a sturdy and secure connection for the pins that allow the bucket to rotate and move with the excavator arm. They help distribute the forces from digging evenly, preventing wear on the pins and reducing the risk of damage to the bucket’s connection points. Without strong pin bosses, the pins could wear out faster, affecting the bucket’s performance and stability.
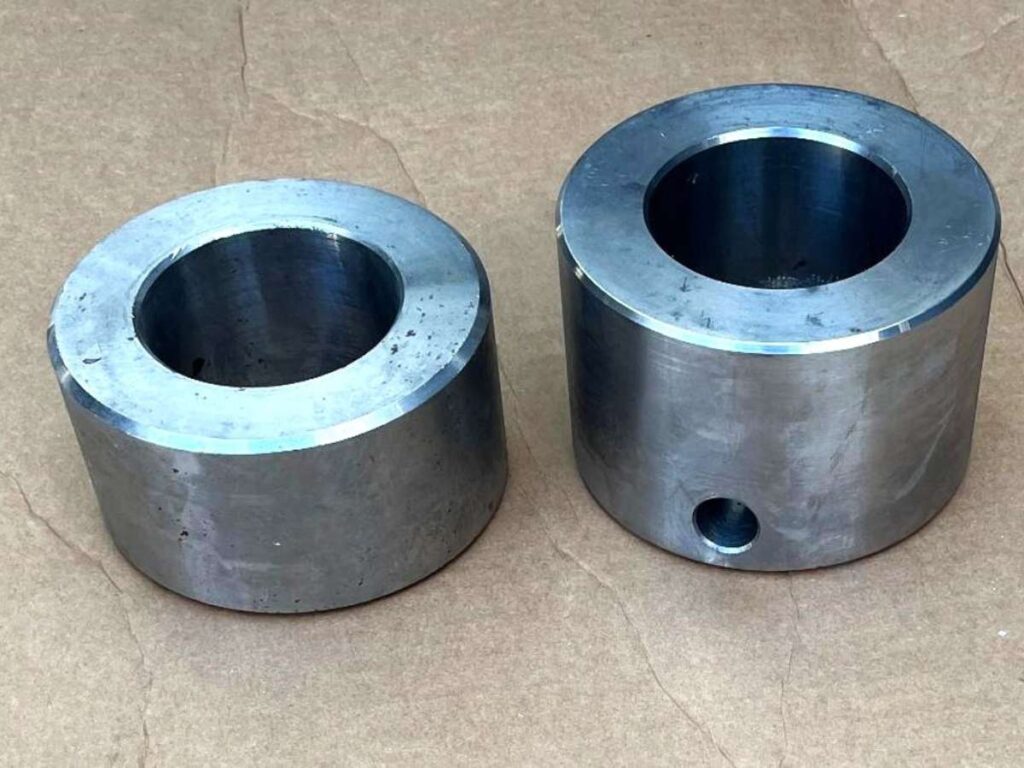
10. Bucket Linkage
The bucket linkage is the mechanism that connects the bucket to the excavator’s hydraulic arm. It consists of several moving parts, including pins and bushings, which help control the movement of the bucket during digging and dumping.
Specifications
- Material: High-strength steel
- Number of Components: Typically 3-5 parts including pins, bushings, and brackets
- Pin Diameter: 2-4 inches
- Length: Varies based on bucket size, usually 12-36 inches
The bucket linkage allows for the controlled movement of the bucket, enabling it to tilt, scoop, and dump materials efficiently. It transfers hydraulic power from the excavator arm to the bucket, providing smooth and precise control during operation. Without a well-functioning linkage system, the bucket would lose its range of motion, making digging and material handling less effective.
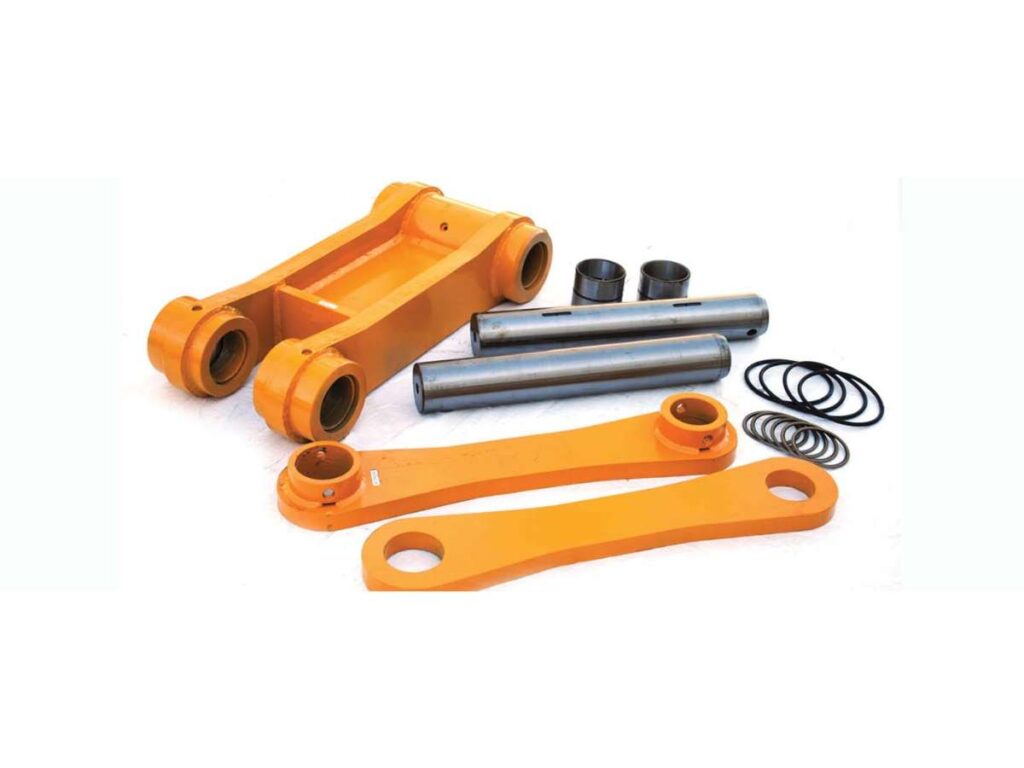
11. Bottom Plate
The bottom plate is the flat surface on the underside of the excavator bucket. It bears the brunt of wear and impact as the bucket scrapes along the ground during digging operations.
Specifications
- Material: High-strength steel or wear-resistant alloy
- Thickness: Typically 1-4 inches
- Width: Matches the width of the bucket, ranging from 36-72 inches
- Length: Extends the full length of the bucket’s bottom
The bottom plate serves as the primary surface that comes in contact with the ground during excavation. It absorbs the pressure and friction from digging, helping to protect the rest of the bucket from wear. A durable bottom plate allows the bucket to slide smoothly over surfaces and contributes to the overall longevity of the bucket by preventing structural damage.
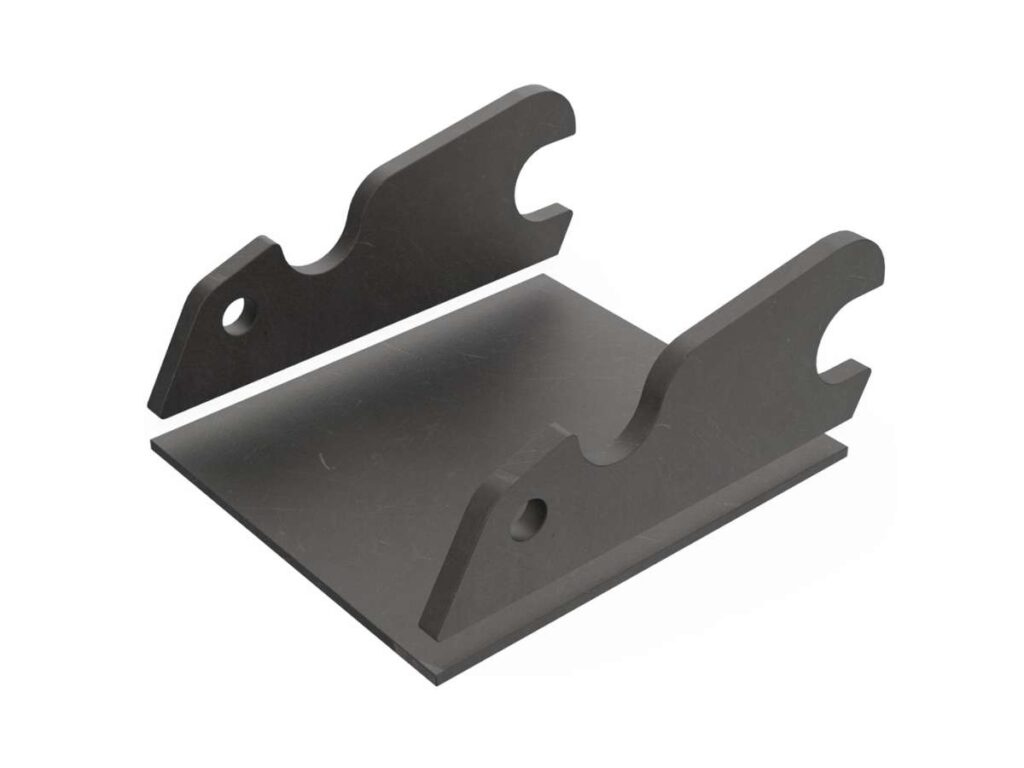
12. Side Plates
Side plates are the vertical steel plates located on both sides of the excavator bucket. They provide structural support and help contain the materials inside the bucket while digging or carrying loads.
Specifications
- Material: High-strength steel or abrasion-resistant alloy
- Thickness: Typically 1-3 inches
- Height: Varies based on bucket size, usually 18-36 inches
- Length: Matches the depth of the bucket
The side plates protect the bucket from damage by absorbing the pressure and friction that occur during side-to-side scraping against materials like soil or rocks. They also help maintain the shape and integrity of the bucket, allowing it to carry a full load without deformation. By reinforcing the bucket’s structure, the side plates contribute to efficient digging and material handling.
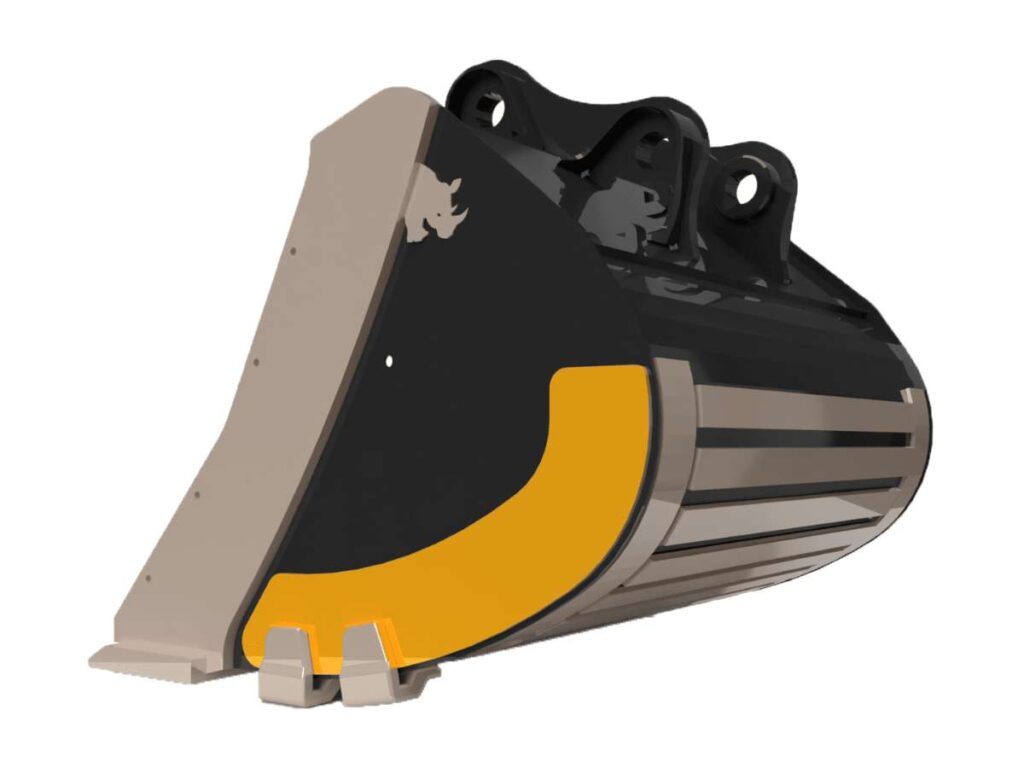
13. Back Plate
The back plate is the rear section of the excavator bucket, connecting the sides and bottom plate while providing structural support. It helps maintain the bucket’s shape and strength, especially when carrying heavy loads.
Specifications
- Material: High-strength steel
- Thickness: Typically 2-4 inches
- Height: Usually matches the height of the side plates, ranging from 18-36 inches
- Width: Corresponds with the width of the bucket (36-72 inches)
Function The back plate serves as the main structural reinforcement for the bucket, helping to distribute the load and stress during heavy digging and lifting. It keeps the bucket stable and aligned with the excavator arm, allowing for smooth movement and effective material handling. Without a strong back plate, the bucket would lose its rigidity, leading to reduced efficiency and potential damage over time.
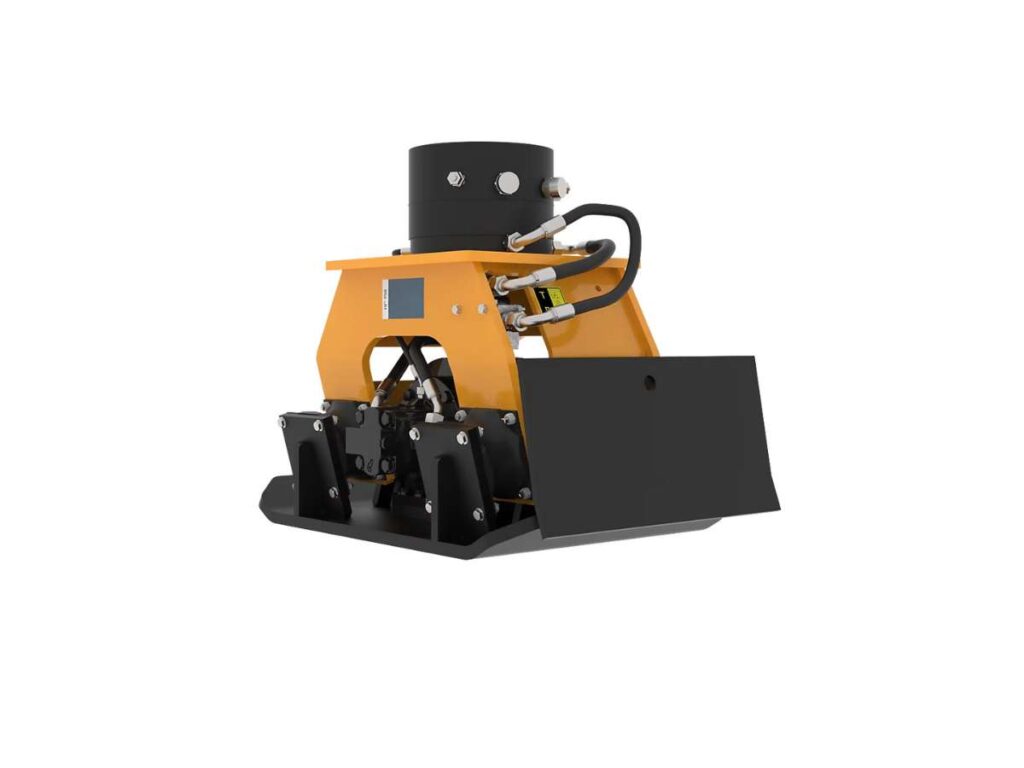
14. Heel Shrouds
Heel shrouds are protective guards installed on the bottom rear corners of the excavator bucket. They help reduce wear on the bucket’s heels, especially during operations that involve heavy scraping or contact with hard surfaces.
Specifications
- Material: Abrasion-resistant steel or alloy
- Thickness: Typically 1-3 inches
- Weight: 5-15 kg per shroud, depending on size
- Mounting Style: Weld-on for a secure fit
Heel shrouds protect the bucket’s rear corners, which are often the first parts to wear out during heavy-duty work. By shielding these high-wear areas, heel shrouds extend the life of the bucket and reduce the need for frequent maintenance or repairs. They also help maintain the bucket’s overall shape, allowing it to continue operating efficiently in tough conditions.
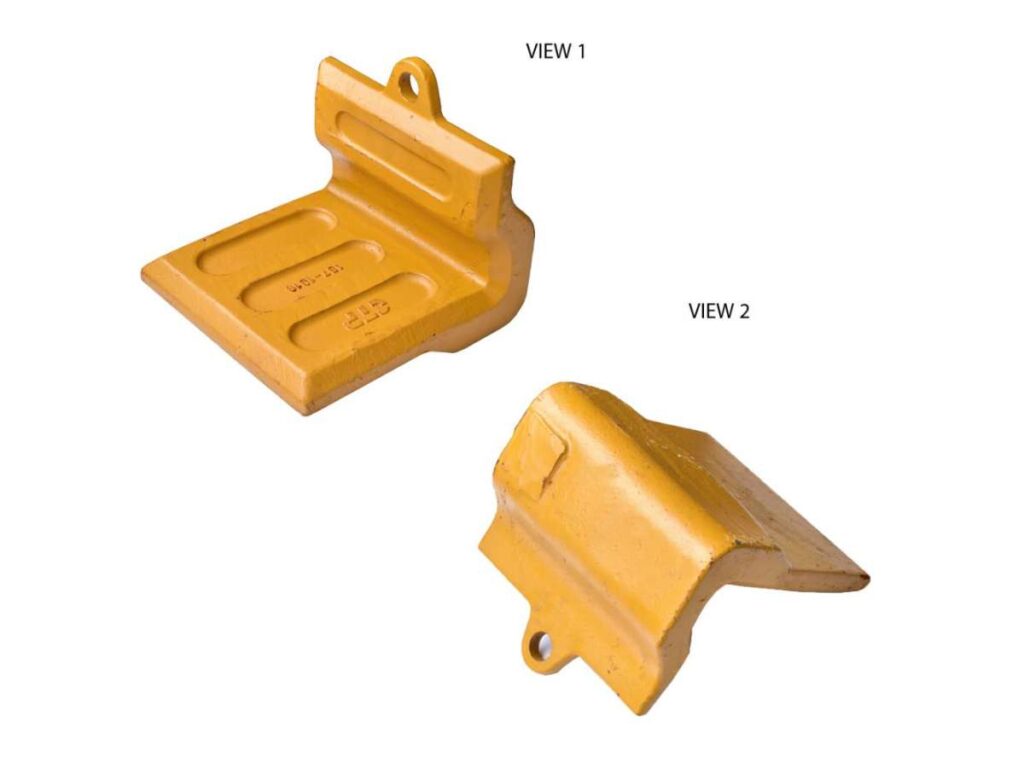
Conclusion
Excavator bucket parts are vital for ensuring your machine runs efficiently and reliably. Each component, from the bucket teeth to the back plate, plays a crucial role in the overall performance of your equipment.
We hope this guide has provided clarity on how these parts function. In the industry, high prices can be a challenge, but EPO offers competitive pricing at 30-60% of big brands without compromising on quality. Contact us today to get top-quality parts that fit your budget and keep your machines running efficiently!